Servo Motor Selection Guide
The selection of servo motors should be based on the characteristics of the driven mechanism, such as the load's moment of inertia on the output shaft, mechanism configuration, efficiency, and friction torque. If these characteristic data are unavailable and no reference cases exist, selecting an appropriate servo motor becomes difficult. In such cases, the first step is to calculate the load inertia and desired rotational acceleration, which will help determine the required acceleration and deceleration torque. Next, the load torque during steady-state motion should be determined by combining the mechanism's mounting configuration and friction torque. Simultaneously, the holding torque required when motion stops—such as the torque needed to counteract gravity in vertical movements—must be calculated. Finally, a suitable servo motor can be selected based on these torque requirements. Each servo motor's specifications include rated torque, maximum torque, and motor inertia, all of which are closely related to load torque and inertia. When selecting a servo motor, its output torque must meet the motion requirements of the mechanism, including acceleration, weight, movement type, etc. While these motion conditions are not directly related to the motor's output power, a higher power rating generally corresponds to greater torque. In summary, both the mechanism weight and its motion conditions influence motor selection. A large inertia or shorter acceleration and deceleration time will require a higher output torque.
MOONS' servo motors
General requirements 10% ≤ km≤ 20% D. Regulation characteristic nonlinearity kv The nonlinearity of the regulation characteristic (kv) is defined as the percentage ratio of speed deviation Δn – which represents the difference between the actual and linear regulation characteristics – under rated excitation voltage and no-load conditions at αk=0.7, relative to the no-load speed n0 at αk=1. The formula is expressed as:
General requirements 20% ≤ kv ≤ 25% E. Locked-rotor characteristic nonlinearity kd The nonlinearity of the locked-rotor characteristic (kd) is defined as the percentage ratio of the maximum torque deviation (ΔTdn)max – which represents the difference between the between actual and linear locked-rotor characteristics under rated excitation voltage, relative to the locked-rotor torque Tds at αk=1. The formula is expressed as:
General requirements kd≤ ±5% F. Electromechanical time constant Tm When rotor resistance is sufficiently large, the mechanical characteristics of AC servo motors approximate a linear relationship. If the mechanical characteristics at αk=1 are approximated by a straight line, the corresponding electromechanical time constant (Tm) follows the same expression as that of a DC servo motor, formulated as:
Wherein, J represents the moment of inertia of the rotor;
ωs denotes the angular velocity under no-load condition in a symmetrical state;
Tds refers to the locked-rotor torque in a symmetrical state. The above outlines the detailed steps for selecting servo motors and the key technical parameters to consider. MOONS' servo motors offer a variety of winding configurations, encoder feedback options, and connector choices. These motors are characterized by high efficiency, low torque ripple, and minimal speed fluctuations. Among them, the MBDV-mini servo motor series features a 20mm frame size with a 30W power rating, while the MBDV servo motor series includes frame sizes of 40mm, 60mm, 80mm, 110mm, and 130mm, covering a power range of 100–1500W. The entire series is CE, RoHS, and UL certifications. For servo motor selection, please contact customer service to select the most suitable model for your application.
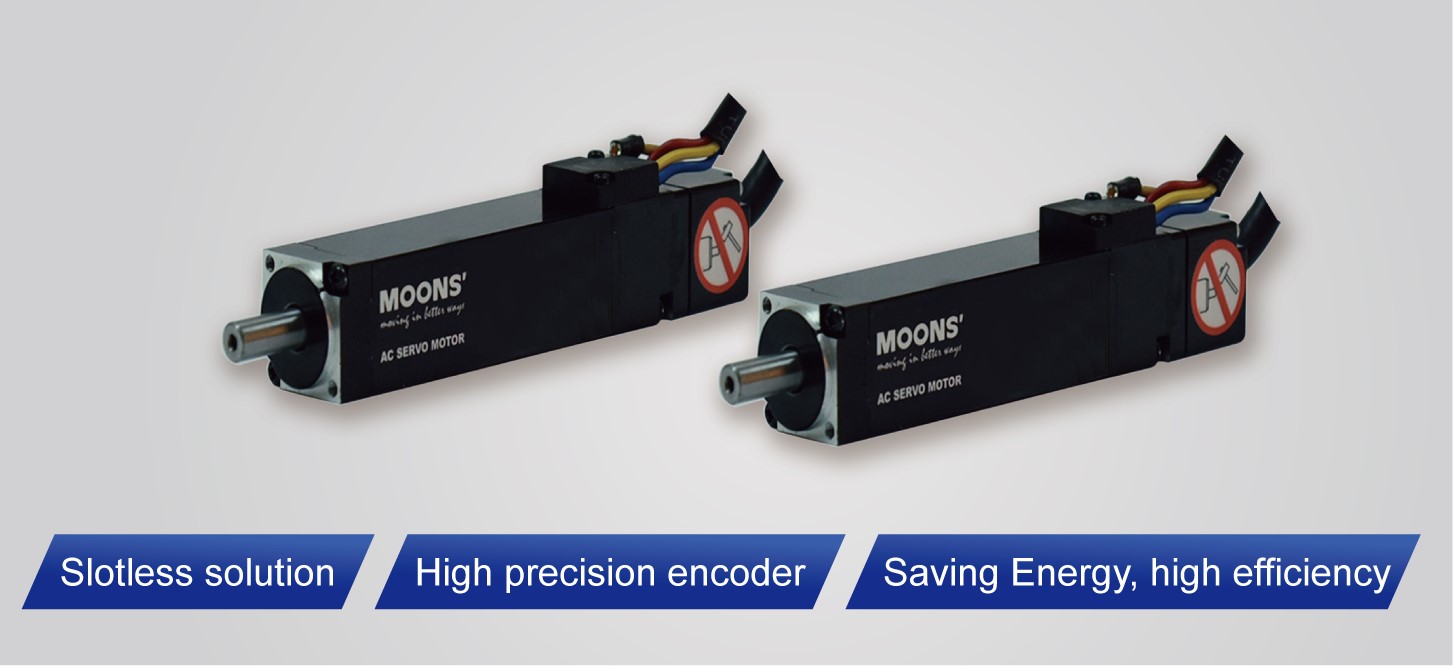
Detailed steps for selecting servo motors
(1) Define the motion requirements of the load mechanism, including acceleration/deceleration speed, motion speed, mechanism weight, and motion profile, etc. (2) Select the appropriate load inertia calculation formula based on the operating conditions, then calculate the load inertia of the mechanism. (3) Preselect a motor specification based on the calculated load inertia and motor inertia. (4) Calculate the acceleration and deceleration torque by combining the preselected motor inertia with the load inertia. (5) Determine the load torque based on the load weight, configuration, friction coefficient, and operating efficiency. (6) Ensure that the maximum output torque of the pre-selected motor is greater than the sum of the acceleration torque and load torque; if the selected model does not meet this requirement, alternative models must be considered and recalculated until a suitable option is found. (7) Calculate the continuous instantaneous torque based on the load torque, acceleration torque, deceleration torque, and holding torque. (8) Verify that the rated torque of the preselected motor exceeds the continuous instantaneous torque. If it does not, alternative models must be considered and recalculated until a suitable option is found. (9) Finalize the servo motor selection by confirming compatibility with the driver and encoder, as well as verifying the mechanical installation space and environmental adaptability.Main technical data of servo motor
When selecting a servo motor, it is also important to consider several key technical parameters.1. Technical data of DC servo motor
A. No-load starting voltage US0 Under rated excitation voltage and no-load conditions, the minimum control voltage required to initiate continuous rotation of the rotor at any position is known as the no-load starting voltage. A lower no-load starting voltage indicates higher sensitivity. This voltage is typically expressed as a percentage of the rated control voltage, generally ranging from 2% to 12%. For low-power motors, US0 tends to be higher. B. Electromechanical time constant Tm Under rated excitation voltage and no-load conditions, the electromechanical time constant is defined as the required for a servo motor to accelerate from rest to 63.2% of its no-load speed after applying a step-rated control voltage. This parameter reflects the motor's dynamic response capability, with smaller values indicating faster response and higher sensitivity. Typically, the electromechanical time constant of servo motors is specified to be less than 0.03s.2. Technical data of AC servo motor
A. No-load starting voltage US0 The no-load starting voltage (US0) is defined as the minimum control voltage required to initiate continuous rotor rotation at any position under rated excitation voltage and no-load conditions. A lower US0 indicates higher motor sensitivity. Typically, US0 should not exceed 3%~4% of the rated control voltage, while for two-phase servo motors used in precision instruments, US0 may be required to be ≤1% of the rated control voltages. B. Stall torque and stall current The locked-rotor torque (TK) refers to the output torque generated when the two-phase stator windings are supplied with rated voltage while the rotor speed remains zero. Under this condition, the currents flowing through the excitation winding and control windings are known as the locked-rotor excitation current and locked-rotor control current respectively. These locked-rotor currents typically represent the maximum current values and serve as key parameters for power supply and amplifier design. C. Mechanical nonlinearity km The mechanical characteristic nonlinearity (km) is defined as the percentage ratio of speed deviation (Δn) – which represents the difference between the actual and linear mechanical characteristics – under rated excitation voltage at any control voltage, measured at torque T=Td / 2, relative to the no-load speed (ns). The formula is expressed as: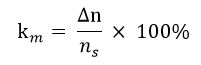
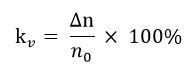
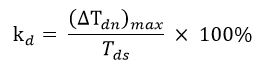
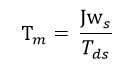
ωs denotes the angular velocity under no-load condition in a symmetrical state;
Tds refers to the locked-rotor torque in a symmetrical state. The above outlines the detailed steps for selecting servo motors and the key technical parameters to consider. MOONS' servo motors offer a variety of winding configurations, encoder feedback options, and connector choices. These motors are characterized by high efficiency, low torque ripple, and minimal speed fluctuations. Among them, the MBDV-mini servo motor series features a 20mm frame size with a 30W power rating, while the MBDV servo motor series includes frame sizes of 40mm, 60mm, 80mm, 110mm, and 130mm, covering a power range of 100–1500W. The entire series is CE, RoHS, and UL certifications. For servo motor selection, please contact customer service to select the most suitable model for your application.