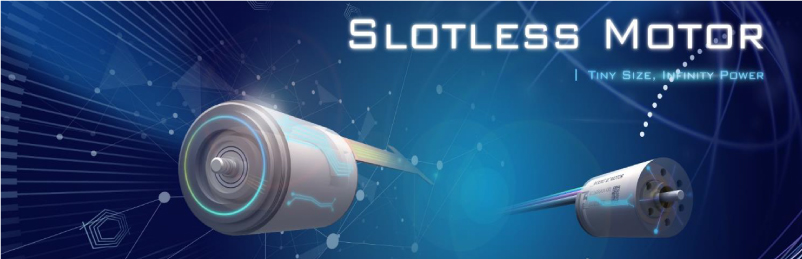
Slotless Brushless DC Motors
With 11 types of winding, theØ13mm series slotless BLDC motors are available in long and short versions with 2 different output powers. MOONS' new micro motions system includes a slotless motor, gearbox, encoder, driver, and mechanical components.
Coreless Brushed DC Motors
Coreless Brushed DC Motors have excellent performance and are easier to control. We provide three types of coreless brushed DC motors whose diameters are 13mm, 17mm, and 24mm, with hollow rotor design, which feature high acceleration, low rotational inertia, no cogging effect, no iron loss, compactness, and lightness.
Slotless/Coreless Motor Drivers
MOONS' slotless and coreless series drive is specially developed for MOONS' slotless and coreless series products, users can achieve fast motor drive through this series of products.
■ Coreless motors Catalog download
![]() | ![]() |
Slotless Coreless Motors Catalog | Driver catalog |
■ Coreless motors Products Videos
MOONS' exhibited slotless and coreless products in Beijing International Medical Equipment Fair in 2019.■ What is a coreless motors?
The coreless motor breaks through the rotor structure of the traditional motor in structure, and adopts an ironless rotor, also called a coreless rotor. By eliminating eddy currents formed by the iron core, this novel rotor structure eliminates power loss. Additionally, the rotor's weight and moment of inertia are greatly reduced, which reduces its mechanical energy loss. Due to the structural change of the rotor, the running characteristics of the motor have been greatly improved, which not only has outstanding energy-saving characteristics but more importantly, has the control and drag characteristics that cannot be achieved by iron core motors. Coreless motors are servo-controlled motors with DC permanent magnets, and can also be referred to as micromotors. The coreless motor has outstanding energy-saving characteristics, sensitive and convenient control characteristics, and stable operation characteristics, and has obvious technical advantages. In many fields, electric motors are being developed as high-efficiency energy conversion devices. | ![]() |
■ Self-supporting winding technology for coreless motors
The self-supporting winding of the coreless is made of enameled wire. The enameled wire is composed of two parts: a copper conductor and an insulating paint layer. After the bare wire is softened by annealing, it is painted and baked many times. During the manufacturing process, the paint on adjacent copper wires is melted together by applying pressure and temperature. Paint is a thermoplastic that contains a solvent that makes it easy to mold. Due to the high-temperature manufacturing process, the solvent gas escapes, the thermoplastic becomes hard, and the winding becomes stable and stiff. The strength and dimensional stability of the wrap can be further enhanced by proper bonding (tape or fiberglass). This is especially important in the case of high current and high load because, in the case of high current and high load, the heating value of the winding increases and the paint becomes softer.■ Classification of coreless motors
Slotless MotorDC brushless cogging motor, commonly known as "brushless coreless" in the industry.
Coreless Motor
DC brushed ironless motor, commonly known as "brush coreless" in the industry.
■ Structural differences between brushed coreless and brushless coreless
The coreless motor is divided into two types: brushed and brushless. There is no iron core in the rotor of the brushed motor, and there is no iron core in the stator of the brushless motor (also known as the Cogged brushless motor). Based on the figure below, the difference between the two motors is that the brushed coreless motor uses a carbon brush (or metal brush) and a commutator for commutation. The brushless coreless motor has no physical structure, the coil wire is directly connected to the controller, and commutation is completed by processing the position signal fed back by the Hall on the connecting plate; the brushed coreless motor is a coil, and the commutator and the connecting plate rotate between the shell and the permanent magnet, and they together form the rotor. The coil of the brushless coreless is fixed, and the permanent magnet rotates in the middle as the rotor. MOONS' has developed brushless coreless motors with frame sizes of φ13mm, φ16mm, φ22mm, and φ30mm. The no-load speed of the motor can reach 15000rpm~50000rpm; φ13mm, φ16mm, φ17mm, φ24mm, and many other frame sizes, the no-load speed of the motor is 10000rpm~16000rpm, the coreless motor can also be used as a torque motor and positional motor after matching with reducers with different speed ratios and encoders with different resolutions The device used for feedback.![]() | ![]() |
Structural diagram of coreless motor | Structural diagram of slotless motor |
■ Features of coreless motor
Features | Advantages |
No cogging | Smooth operation at low speed No cogging, Low vibration, low noise Rotor can be controlled in any position |
Compact structure | Better magnetic circuit design Higher power density Low temperature rise, high efficiency |
Low inductance | High dynamic response High acceleration |
■ Advantages of coreless brushed dc motors
High efficiency and energy utilization: The coreless motor eliminates the iron core structure, reduces stator iron loss and rotor eddy current loss, and has extremely high energy conversion efficiency, with energy utilization between 75% and 90%High speed and dynamic response: Since the rotor has no iron core, the moment of inertia is small, and the mechanical time constant can reach the millisecond level, which is suitable for high-speed operation and fast response application scenarios. This design enables the motor to start and brake quickly, with excellent dynamic response performance
High power density: The coreless motor has a compact design and can provide greater torque output in a limited space, suitable for application scenarios that require high power density
Low noise: The brushless coreless motor generates less noise during operation, suitable for environments that require quiet operation
High precision and controllability: Due to its structural design, the coreless motor has high precision and controllability, suitable for applications that require precise position control
Long life and low maintenance cost: The use of advanced commutation technology reduces physical contact and wear, extends the life of the motor, and reduces maintenance costs
■ Advantages of slotless brushless dc motors
High working efficiency: slotless brushless dc motor uses copper coil, no winding and slot silicon steel sheet are required, eddy current and hysteresis loss are reduced, and the smaller resistance further reduces energy loss and improves working efficiencyHigh power density: due to its slotless design, the volume and weight are reduced, the copper coil is light and the eddy current loss is low, making the output power and torque higher, thus achieving high power density
No cogging effect and torque lag: the design of copper coil and no silicon steel sheet eliminates the cogging effect, reduces the fluctuation of speed and torque, avoids torque lag, and improves the response and stability of the motor
Low starting torque: due to the lack of cogging effect and hysteresis loss, the starting torque is low, the main obstacle is the bearing load, and it is easy to start
No radial force between the rotor and the stator: the design without stationary silicon steel sheet makes the rotor and the stator have no radial magnetic force, which enhances the rotation The running stability of the motor is suitable for precision control occasions.
Low noise: The elimination of slotted silicon steel sheets reduces torque and voltage harmonics, reduces noise during motor operation, and makes the motor run more smoothly and with less noise.
Fast response: The copper coil with low inductance makes the current react faster to voltage changes, and the rotor without iron core reduces the moment of inertia, which improves the response speed and acceleration.
High torque: The slotless brushless dc motor performs well in peak torque, and the current and torque are linearly related, ensuring stable torque output.
Smooth sine waveform: The precise placement of the copper coil and the application of the sine wave drive controller ensure the smoothness of the voltage waveform and improve the accuracy of torque control. It is suitable for equipment that requires precise control.
Good heat dissipation effect: The copper coil design optimizes the air flow on the inner and outer surfaces, which is more conducive to heat dissipation than traditional motors, improving the operating efficiency and life of the motor.
■ Industry application of coreless motor?
As the coreless motor avoids various technical drawbacks of the iron core motor, and its outstanding features are concentrated in its main performance, it has a wide range of applications. With the rapid development of industrial technology, higher expectations for the servo characteristics of motors are continually being raised, making coreless motors irreplaceable in many applications.Since coreless motors entered the large industrial and civil fields from the military and high-tech fields, especially in industrialized countries, they have been used in virtually all industries and have impacted most products.
1. Fast-response follow-up system. With its rapid adjustment of the missile's flight direction, follow-up control of a high-magnification optical drive, rapid automatic focusing, highly sensitive recording and detection equipment, industrial robots, bionic prostheses, etc., the coreless motor can easily meet its technical requirements.
2. Driving components that require smooth and long-lasting drag. The power supply time can be more than doubled with the same power supplies for portable instruments, personal portable equipment, field equipment, etc.
3. Various aircraft, including aviation, aerospace, model aircraft, etc. As a result of the lightweight, small size, and low energy consumption of the coreless motor, the aircraft's weight can be greatly reduced.
4. As well as optical instruments, medical equipment, robots, etc., subdivided applications include dental equipment, micro-pumps, infrared lenses, pipetting modules, grippers, robotic hands, dispensing valves, surgical tools, etc.
![]() Factory automation | ![]() Artificial intelligence | ![]() Medical |
![]() Laboratory automation | ![]() Aerospace | ![]() Measurement |