* Free shipping to North America and most of Europe for orders of $100 or more
ID M2DC Series Servo Drives
DC Input Servo Drive, Servo Solutions for DC power supply and Battery supply● Easy to use online Auto-tuning
● Internal regeneration resistor
● Stored program execution---Q Program



- current tab: Description & Feature
- Data Sheet
- Online Ordering
- Torque Speed Curves
- Dimension
- Downloads
- Recommended Options
- Delivery & Packaging
![]() |
Before auto-tuning After auto-tuning |
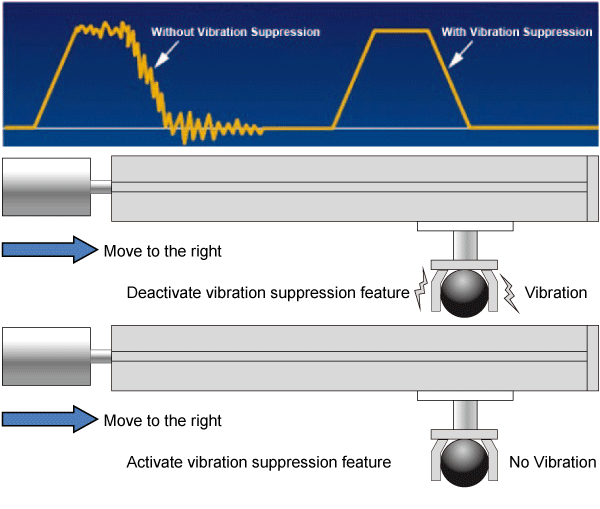
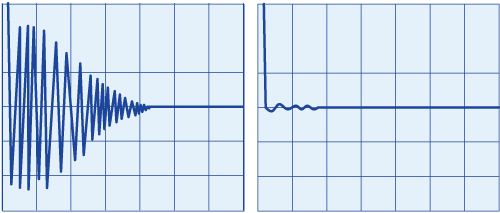
Safe Torque Off (STO) is a hardware level safety protection function. When the STO function is activated, the drive’s hardware circuitry automatically forces all power transistors OFF to cut off the motor current, immediately disable motor operation and prevent unexpected restarting. The operator isn’t required to physically shut off the electromagnetic contactor to ensure personal and equipment safety in case of an emergency.
● Open Collector Pulse Input: 500KHz, 5-24VDC
● Differential Line Input: 2MHz, 5VDC
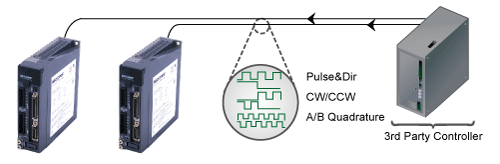
● Support analog position, analog velocity and analog torque control
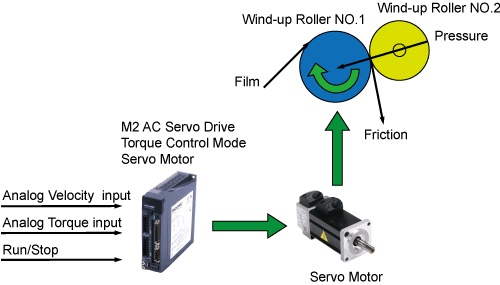
Q Programmer is MOONS’ own single-axis motion control software based on SCL commands. It can be used to create sophisticated and functional programs that can be saved to a drive’s nonvolatile memory, and then run standalone, or without a permanent connection to the host. Q drives offer a high level of flexibility and functionality to the machine designer and system integrator.
Features:
• Motion control commands (relative position, absolute position, homing mode, etc.)
• Multi-tasking
• Conditional Processing (external I/O, internal command)
• Math Calculation (+, -, *, /, &, or)
• Data register manipulation
• Logic motion command (loop, call functions)
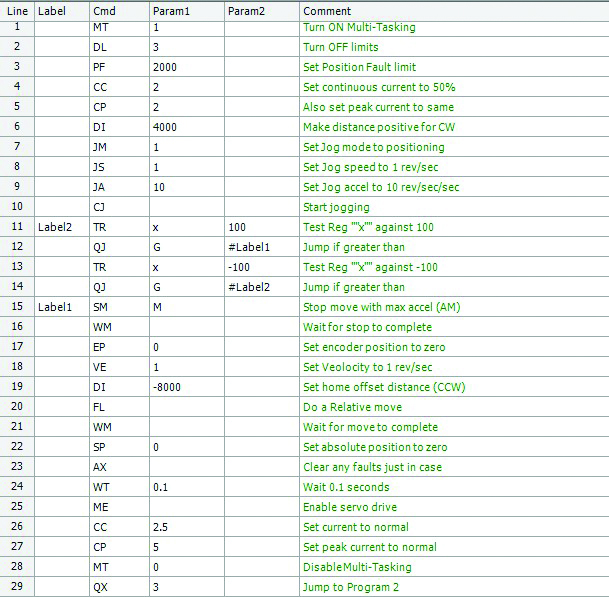
![]() | ![]() | ![]() | ![]() |
Items | Specification |
---|---|
Physical Layer Standard | RS-232, RS-485, Ethernet |
Communication Protocol | Modbus/RTU, Modbus/TCP |
Bus Connector | RJ11(RS-232), RJ45(RS-485, Ethernet) |
Baud Rate | RS-232/485: 9600bps, 19200bps, 38400bps, 57600bps, 115200bps Ethernet: 10/100Mbps |
Control Mode | Position Mode, Velocity Mode, Torque Mode, Homing Mode |
eSCL is based on MOONS’s SCL for commanding and querying motion control products over Ethernet.
Items | Specification |
---|---|
Physical Layer Standard | RS-232, RS-485, Ethernet |
Communication Protocol | SCL, eSCL |
Bus Connector | RJ11(RS-232), RJ45(RS-485, Ethernet) |
Baud Rate | RS-232/485: 9600bps, 19200bps, 38400bps, 57600bps, 115200bps Ethernet: 10/100Mbps |
Control Mode | Position Mode, Velocity Mode, Torque Mode, Homing Mode |
Items | Specification |
---|---|
Physical Layer Standard | Ethernet |
Communication Protocol | EtherNet/IP |
Bus Connector | RJ45 |
Baud Rate | Ethernet: 10/100Mbps |
Control Mode | Position Mode, Velocity Mode, Torque Mode, Homing Mode |
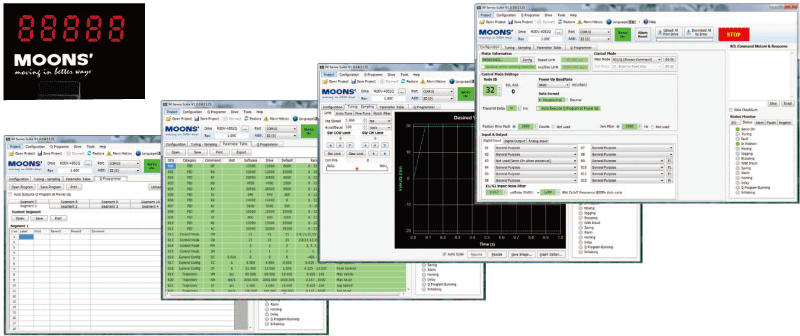
• Set and query parameters
• LED display of drive status
M Servo Suite tuning software
• Friendly interface
• Easy set-up
• Drive set-up and configuration
• Easy to use on-line auto-tuning
• Built in oscilloscope for motion testing and monitoring
• Write and save SCL scripts
• Four 5-24VDC high speed inputs, maximum input frequency 500KHz, with digital input filter
• Eight optically isolated multi function inputs, 5-24VDC, 20mA
• Six Digital outputs, maximum 30VDC 30mA
• Two analog inputs
• Linear Motion, Rotary Motion
• Linear Motion: up to 63 position points controlled by different input signal combinations
• Rotary motion: up to 48 position points per revolution
• Configurable acceleration/deceleration speed settings for each individual point
• Multi position control with no pulse input requirement
Applications: Linear Module, Rotary Table, Index Plate, Tool Changing System
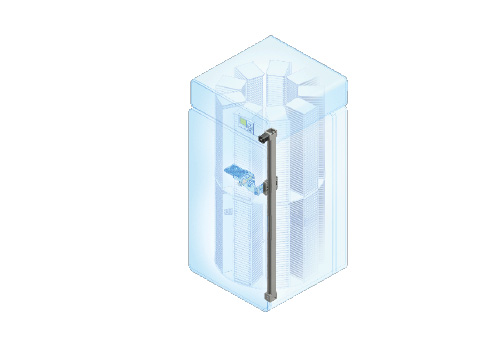
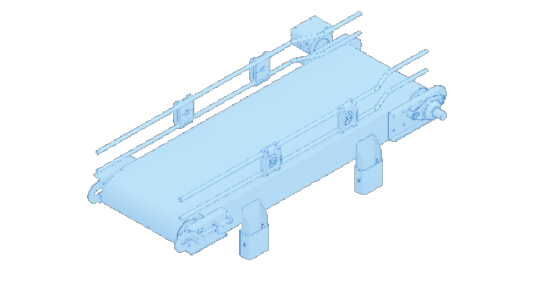
• Set up to 8 different velocities via different I/O combinations
• Use digital input signal for settings, with no analog input requirement
• Velocity configuration via both M Servo Suite and control panel
• Programmable acceleration and deceleration settings for each individual velocity change
Applications: Polish Machine, Conveyor
For applications with varying loads, gain selection allows the M2 servo drive to optimize the motor’s overall performance.
Applications: X-Y Robot Arm, Vertical Conveyor
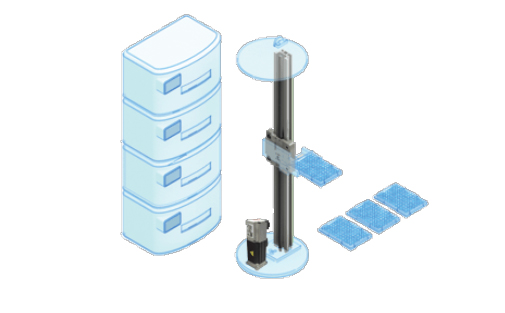
When the pulse inhibit signal is triggered, the motor will stop moving regardless of pulse inputs.
Applications: Packaging Machinery
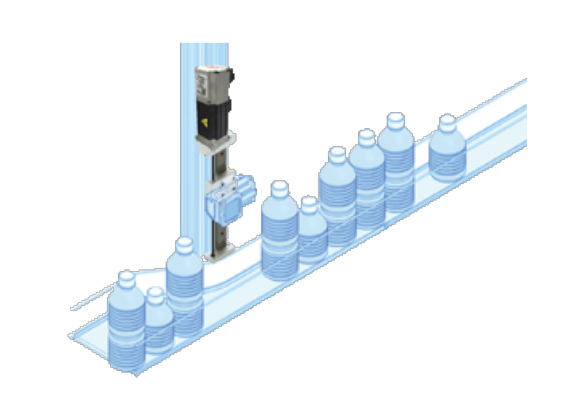
■ Servo Drive Numbering Information
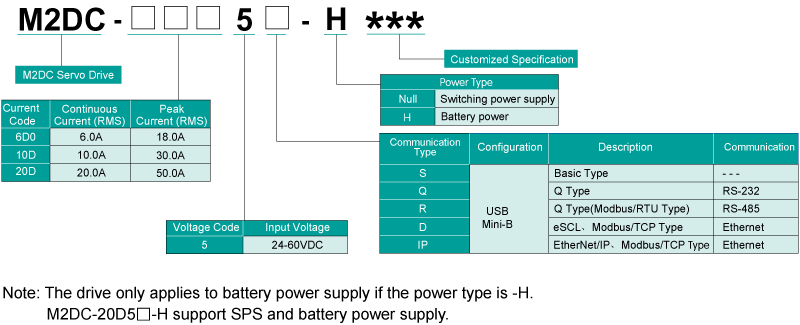
■ Servo Motor Numbering Information
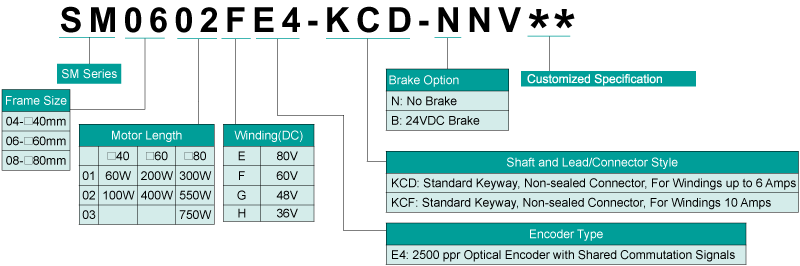
■ System Configration
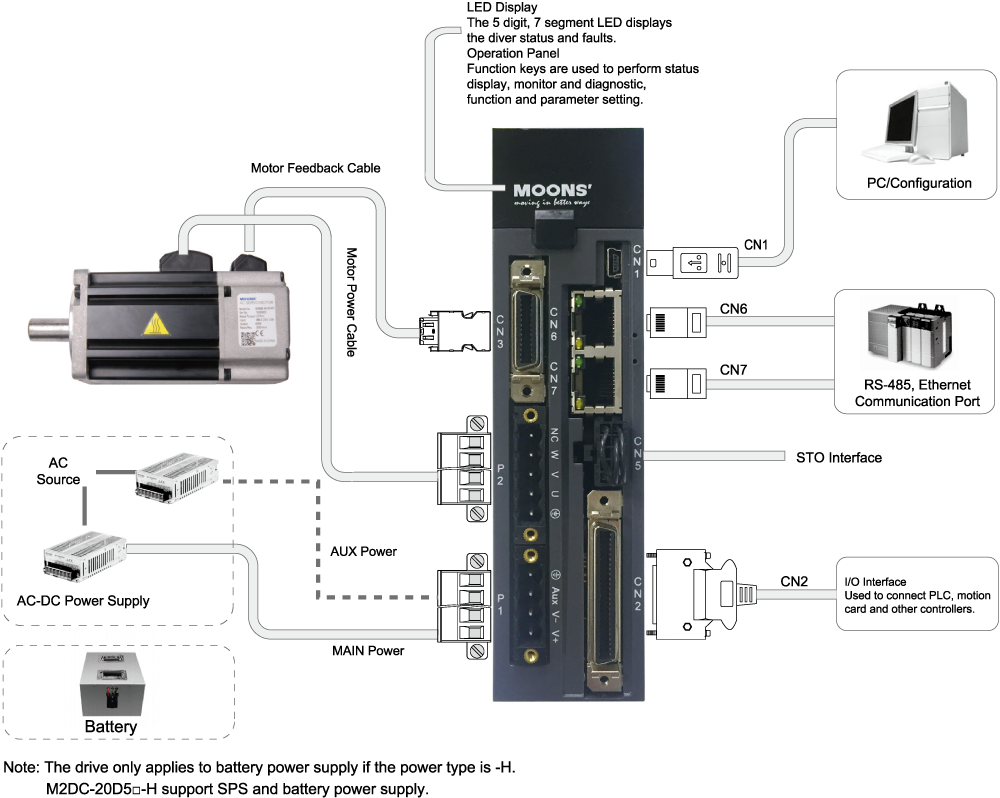
■ Drive Motor Matching Table
Servo Drive | |||||
---|---|---|---|---|---|
Basic Type | M2DC-6D05S | M2DC-10D5S | M2DC-20D5S | ||
Q Program Type (RS-232 Communication) | M2DC-6D05Q | M2DC-10D5Q | M2DC-20D5Q | ||
Q Program Type (RS-485 Communication) | M2DC-6D05R | M2DC-10D5R | M2DC-20D5R | ||
eSCL | M2DC-6D05D | M2DC-10D5D | M2DC-20D5D | ||
EtherNet/IP* | M2DC-6D05IP | M2DC-10D5IP | M2DC-20D5IP | ||
Matching Motor | |||||
Matching Motor | 40 Frame, 60W, 100W | 60 Frame, 200W, 400W | 80 Frame, 300W, 550W | 80 Frame, 750W | |
Without Brake | SM0401HE4-KCD-NNV SM0402FE4-KCD-NNV | SM0601GE4-KCF-NNV SM0602FE4-KCF-NNV SM0602GE4-KCF-NNV SM0602GE4-KCF-NNV-M | SM0801GE4-KCF-NNV SM0802EE4-KCF-NNV | SM0803GE4-KCF-NNV SM0803GE4-KCF-NNV-M | |
With Brake | SM0401HE4-KCD-BNV SM0402FE4-KCD-BNV | SM0601GE4-KCF-BNV SM0602FE4-KCF-BNV SM0602GE4-KCF-BNV | SM0801GE4-KCF-BNV SM0802EE4-KCF-BNV | SM0803GE4-KCF-BNV SM0803GE4-KCF-BNV-M | |
Gearhead Motor | |||||
Without Brake | SM0401HE4-KCD-NNV-PG**A SM0402FE4-KCD-NNV-PG**A | SM0601GE4-KCF-NNV-PG**A SM0602FE4-KCF-NNV-PG**A | SM0801GE4-KCF-NNV-PG**A SM0802EE4-KCF-NNV-PG**A | - | |
With Brake | SM0401HE4-KCD-BNV-PG**A SM0402FE4-KCD-BNV-PG**A | SM0601GE4-KCF-BNV-PG**A SM0602FE4-KCF-BNV-PG**A | SM0801GE4-KCF-BNV-PG**A SM0802EE4-KCF-BNV-PG**A | - | |
* For the latest details, Please contact our company. ** Standard gear ratios are 5:1; 10:1 and 20:1. | |||||
Accessories (Requiste) | |||||
IO Connector | M2-50P | ||||
USB mini-B Configuration | 2620-150 | ||||
Standard* Cable | Motor power | 1630-X00 | 1627-X00 | 1641-X00 | |
Encoder | 2627-X00 | ||||
Brake *** | 1602-X00 | ||||
Flexible** Cable | Motor power | 1631-X00 | 1628-X00 | 1642-X00 | |
Encoder | 2621-X00 | ||||
Brake *** | 1602-X00-C05 (Note) | ||||
*** It is a requisite when selecting a motor with brake. Note: Please contact us when you select flexible brake cable. |
■ Drive Specification
Input Power | M2DC-6D0 M2DC-10D M2DC-20D | Main Circuit | 20~60VDC |
---|---|---|---|
Auxiliary power supply | 10~60VDC | ||
Withstand Voltage | Primary to earth: withstand 500 VAC, 1 min | ||
Environment | Temperature | Ambient temperature: 0°C to 50°C(If the ambient temperature of servo drive is higher than 40°C, please install the drive in a well-ventilated location) Storage temperature: -20°C to 65°C | |
Humidity | Both operating and storage: 10 to 85%RH or less | ||
Altitude | Lower than 1000m | ||
Vibration | 9.8m/s2 or less, 10 to 60Hz (Do not use continuously at resonance frequency) | ||
Control Method | PWM Sinusoidal wave drive | ||
Encoder Feedback | 2500line incremental optical encoder | ||
I/O | Digital Signals | Input | 8 optical isolated multi function inputs, 5-24VDC, 20mA 2 optical isolated multi function high speed inputs, 5-24VDC, 20mA |
Output | 6 optical isolated multi function outputs, 30VDC, 20mA | ||
Analog Signals | Input | 2 inputs (12Bit A/D : 2 input) | |
Pulse Signal | Input | 2 Photo-coupler inputs: 5 ~ 24V, minimum pulse width 1μs, max. pulse frequency 500KHz 2 Line receiver inputs: 5V differential signal, minimum pulse width 0.25μs, max. pulse frequency 2MHz | |
Output | 4 outputs ( Line driver: 3 outputs, open collector: 1 outputs) | ||
Communication | USB Mini-B | Connection with PC or 1 : 1 communication to a host. | |
RS232 | RS-232 Communication | ||
RS485 | RS-485 Communication & Modbus/RTU | ||
Ethernet | EtherNet/IP,Modbus/TCP,eSCL | ||
Front panel | 4 keys (MODE, UP, DOWN, SET) , 5-digit LED Display | ||
Regeneration Resistor | Built-in regenerative resistor 20W | ||
Control Mode | (1) Position mode (2) Analog Velocity mode (3) Analog Position mode (4) Analog Position mode (5) Velocity Change mode (6) Command Torque mode (7) Command Velocity mode (8) Position Tables | ||
Control Input Signal | (1) Servo-ON input (2) Alarm clear input (3) CW/CCW Limit (4) Pulse& Direction or CW/CCW input (5) Gain Switch (6) Control mode Switch (7) Pulse Inhibition (8) Gear switch (9) Velocity Change mode (10) Analog input (11) General input | ||
Control Output Signal | (1) Alarm output (2) Servo-Ready output (3) External brake release (4) Speed reached output (5) Torque reached output (6) Position reached output (7) TachOut (8) Servo-on status output (9) General output | ||
Certification | RoHS, EN 61800-3, EN 61800-5-1 | ||
Drive Mass | M2DC-6D0: 0.59kg M2DC-10D: 0.59kg M2DC-20D: 0.61kg |
■ Motor Specifiction
Encoder Type | 2500ppr Incremental encoders |
---|---|
Insulation Class | Class B (130℃ ) |
IP65 Rating | IP65 (Incremental encoder) |
Installation Iocation | Indoor installation, avoiding direct sunlight, corrosiveand flammable gas |
Ambient Temperature | Operating 0 to 40°C, Storage -20 to 80°C |
Ambient Humidity | Operate where the relative humidity range is 20% to 85% and non-condensing |
Elevation | Operating 1,000m |
Vibration | 49m/s2, 10Hz-60Hz (DO NOT use the drive for extended periods of time at the resonance point.) |
■ Holding Brake Option
With no power, a spring presses a friction plate into a stationary plate, whitch produces holding torque. When power is applied to the brake coil, the brake solenoid pulls the friction plate away from the stationary plate, whitch allows the motor to turn.
Model | 40mm | 60mm | 80mm | ![]() |
---|---|---|---|---|
Static friction torque (Nm) | 0.32Nm | 1.5Nm | 3.2Nm | |
Rated Voltage (VDC) | 24VDC | |||
Power W(20℃) | 6.9 | 7.2 | 10 | |
Rated Current (A) | 0.29 | 0.3 | 0.42 | |
Brake Time | Standard air gap, below 20℃<25ms | |||
Release Time | <25ms | |||
Release Voltage | 18.5VDC max.(at 20℃) |
■ Shaft Seal
The oil seal will produce a certain resistance to the motor shaft, about 10% torque will be lost.
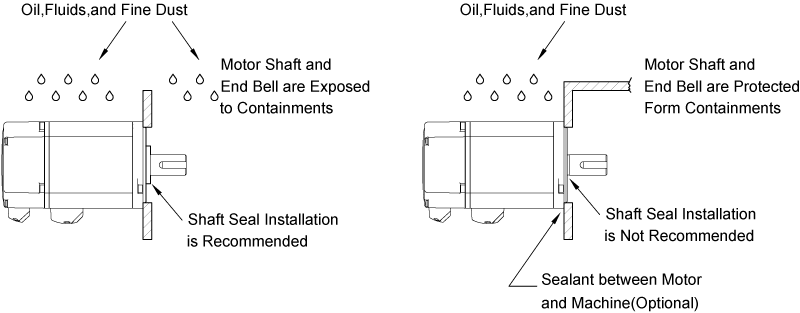
Compare | Item | Price (USD) |
Buy Now |
---|---|---|---|
|
M2DC-6D05S | $359.00 |
Added to Your Shopping Cart
|
|
M2DC-6D05Q | $426.00 |
Added to Your Shopping Cart
|
|
M2DC-6D05R | $426.00 |
Added to Your Shopping Cart
|
|
M2DC-6D05D | N/A | |
|
M2DC-6D05IP | N/A | |
|
M2DC-10D5S | $362.00 |
Added to Your Shopping Cart
|
|
M2DC-10D5Q | $431.00 |
Added to Your Shopping Cart
|
|
M2DC-10D5R | $431.00 |
Added to Your Shopping Cart
|
|
M2DC-10D5D | N/A | |
|
M2DC-10D5IP | N/A | |
|
M2DC-20D5S | N/A | |
|
M2DC-20D5R | N/A | |
|
M2DC-20D5S-H | N/A | |
|
M2DC-20D5Q-H | N/A | |
|
M2DC-20D5R-H | N/A | |
|
M2DC-20D5D-H | N/A | |
|
M2DC-20D5IP-H | N/A |
■ Low Inertia Motor—Frame 40mm/60mm/80mm
■ Medium Inertia Motor—Frame 60mm/80mm
■ Drive Dimensions (Unit: mm)
■ Low Inertia Motor(Unit: mm)
□ Frame 40mm
Without Brake | L |
---|---|
SM0401HE4-KCD-NNV | 92 |
SM0402FE4-KCD-NNV | 109 |
With Brake | L |
---|---|
SM0401HE4-KCD-BNV | 129 |
SM0402FE4-KCD-BNV | 147 |
□ Frame 60mm
Without Brake | L |
---|---|
SM0601GE4-KCF-NNV | 105 |
SM0602FE4-KCF-NNV | 125 |
SM0602GE4-KCF-NNV | 125 |
With Brake | L |
---|---|
SM0601GE4-KCF-BNV | 145 |
SM0602FE4-KCF-BNV | 165 |
SM0602GE4-KCF-BNV | 165 |
□ Frame 80mm
Without Brake | L |
---|---|
SM0801GE4-KCF-NNV | 101 |
SM0802EE4-KCF-NNV | 116 |
With Brake | L |
---|---|
SM0801GE4-KCF-BNV | 148 |
SM0802EE4-KCF-BNV | 163 |
Without Brake | L |
---|---|
SM0803GE4-KCF-NNV | 130.8 |
With Brake | L |
---|---|
SM0803GE4-KCF-BNV | 178 |
■ Medium Inertia Motor(Unit: mm)
□ Frame 60mm
Without Brake | L |
---|---|
SM0602GE4-KCF-NNV-M | 135 |
With Brake | L |
---|---|
SM0602GE4-KCF-BNV-M | 175 |
□ Frame 80mm
Without Brake | L |
---|---|
SM0803GE4-KCF-NNV-M | 140.8 |
With Brake | L |
---|---|
SM0803GE4-KCF-BNV-M | 188 |
■ Gearhead Servo Motor(Unit: mm)
□ Frame 40mm
□ Frame 60mm
□ Frame 80mm
Title | Type | Size(KB) | Download |
---|---|---|---|
M2DC-20D5□.pdf | 39 | ||
M2DC-10D_2D Drawing.pdf | 101 | ||
M2DC-10D_2D Drawing.dwg | DWG | 551 | |
M2DC-6D0_2D Drawing.pdf | 101 | ||
M2DC-6D0_2D Drawing.dwg | DWG | 551 |
Title | Type | Size(KB) | Download |
---|---|---|---|
M2DC-10D_3D Model.step | STEP | 6242 | |
M2DC-20D5□.step | STEP | 2149 | |
M2DC-6D0_3D Model.step | STEP | 6242 |
Title | Type | Size(KB) | Download |
---|---|---|---|
Modbus RTU Manual_EN20171018.pdf | 1470 | ||
M2DC Series_User Manual.pdf | 5785 | ||
HOST COMMAND reference uesr manual.pdf | 6963 | ||
CANopen Manual Rev 1.2.pdf | 3833 |
Title | Type | Size(KB) | Download |
---|---|---|---|
Low Voltage Family Brochure_EN2022-L.pdf | 8361 |
Title | Type | Size(KB) | Download |
---|---|---|---|
M2DC Series_Quick start.pdf | 2423 |
Title | Type | Size(KB) | Download |
---|---|---|---|
M2DC Series_CE.rar | 983 |
Title | Type | Size(KB) | Download |
---|---|---|---|
RS485 Bus Utility Setup 1.0.18.0510.rar | RAR | 1898 | |
CANopen Test Tool Setup 1.0.23.0506.zip | ZIP | 10024 | |
M Servo Suite Setup 1.0.21.1010.zip | ZIP | 28894 | |
M2 EtherNetIP _r3.03.eds | EDS | 76 | |
CAN_EDS_212E_M2.eds | EDS | 45 |
Filter By Product Type
All ProductsIO Connector
USB Configuration
Matching Motor
Motor Power Cable

Delivery & Packaging
Ensure your ordered products are always safely packaged from easy click to fast delivery to your handsProfessional Product Label
Considering all possible harsh application environments, MOONS' specially designed labels for each product, which pass water-resistance test, durability rub test, high temperature resistance and corrosion resistance tests.Besides, our product labels are attached with QR code linking to product details, which is convenient for clients to view the detail product page with their mobile phones.
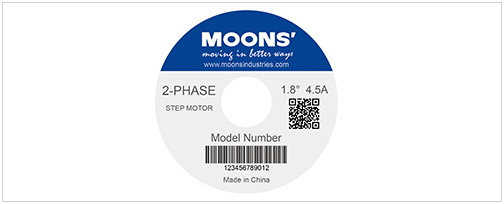
Note: This label design is suitable for products of stepper motor.
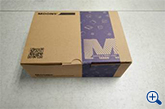
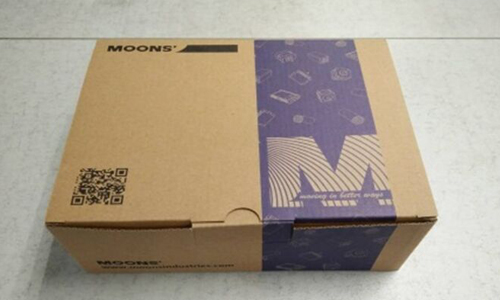
(Professional packing box and unique appearance design)
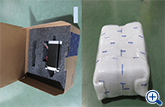
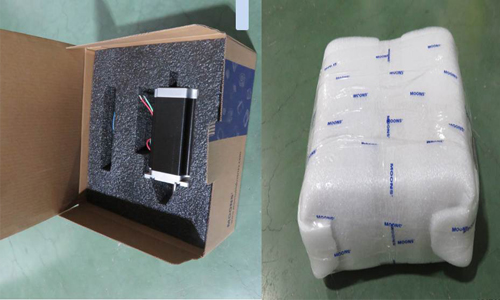
(Single item packed with EPE)
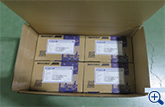
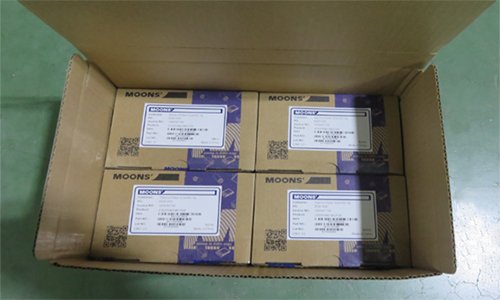
(Multi-products packed with another box)
Safely Packaging
In order to ensure your shipments withstand the long trip and arrive safely and intact, MOONS' specially designed Individual package to pass the drop test with its stable structure.Besides,the package is made from recyclable materials, providing you with professional safety delivery.
Whether just single item or multi-products the clients buy, all products are packed twice to avoid the damage further.
Shipping Visualization
For each case, products are carefully packed by experienced warehouse staff and the key processes are recorded by photos, which are then posted on our website, so that clients could clearly know the packing process and logistics status after placing order.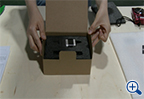
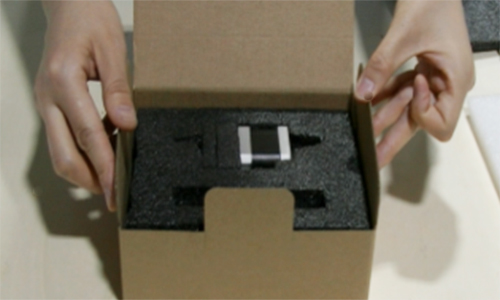
(Product in the box)
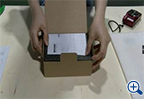
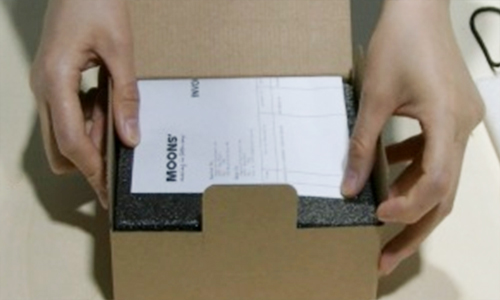
(Add the invoice)
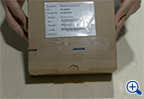
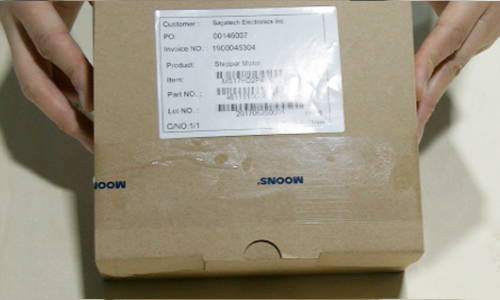
(Label the commodity)
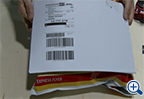
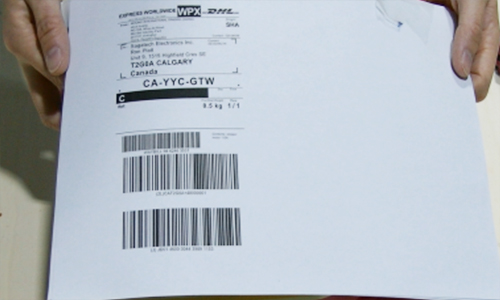
(The logistics waybill attached)
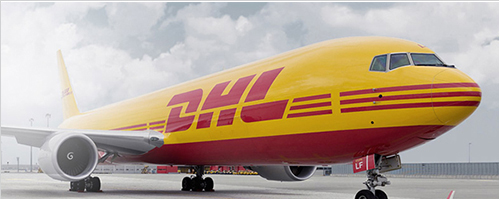
Fast Delivery
Fast Cross-Border DeliveryMOONS' chooses DHL as our main international express shipping partner. As the world's leading logistics specialist, DHL provides our customers with fast and professional inter- national door-to-door delivery service.
Estimated Delivery Time: e.g. China-USA major cities 3 business days.
Professional
Warehouse Management
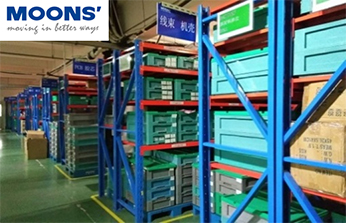