* Free shipping to North America and most of Europe for orders of $100 or more
* From May. 1 - May. 5, Online Orders Shipping will be postponed during Labour Day and resume on the first working day – May. 6. Thanks for your patience!
ID SSDC Series Step-Servo Drives
SSDC series is a high performance, intelligent Step-Servo system (Closed-Loop Stepper System) for multi-axes field bus control, Supporting pulse/direction control, analog control and multiple field bus controls such as Modbus, CANopen, SCL/eSCL commands, EtherNet/IP and EtherCAT protocol. And SSDC series also supports Stand-alone Programmable Function(Q programmer).● Support Multi-axis Fieldbus Control
● Closed-loop Stepper System with Servo Technology
● Low Vibration, Low Noise, Low Heat
● Compact Size, High Torque, Long Working Life
● High Efficiency, High Precision, High Response
● Optimized interface orientation for easy wiring(SSDC06-EC-H)



- current tab: Description & Feature
- Data Sheet
- Online Ordering
- Torque Speed Curves
- Dimension
- Downloads
- Recommended Options
- Delivery & Packaging
■ Multi-functional Capability
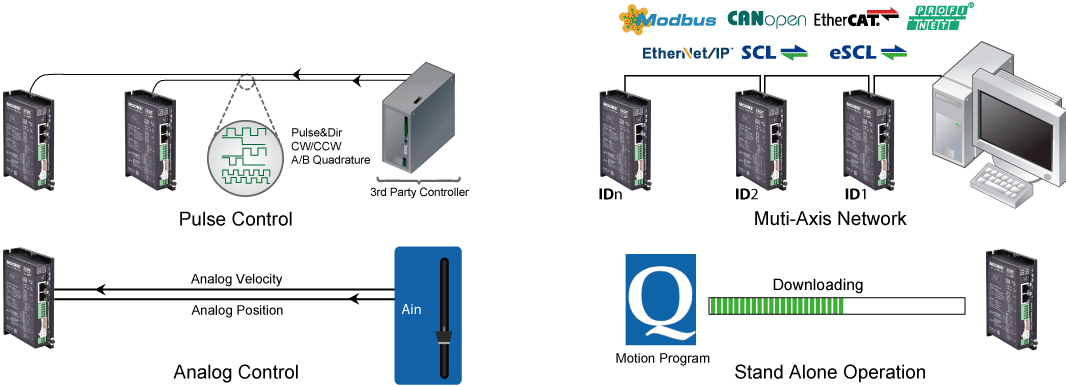
■ Closed-Loop Control
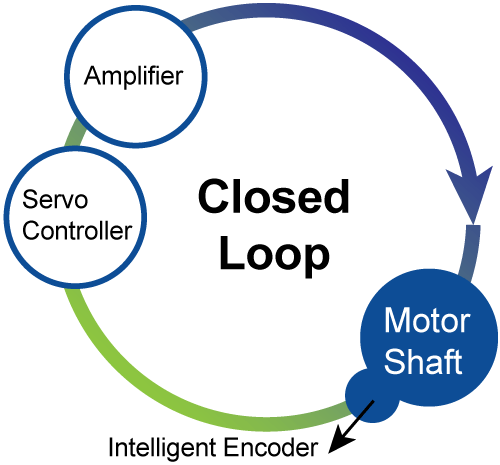
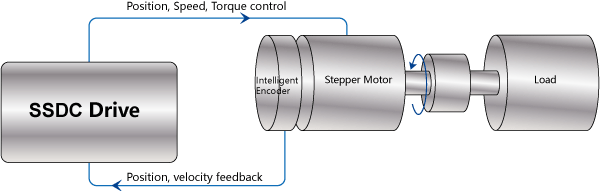
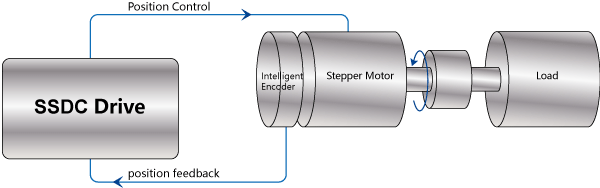
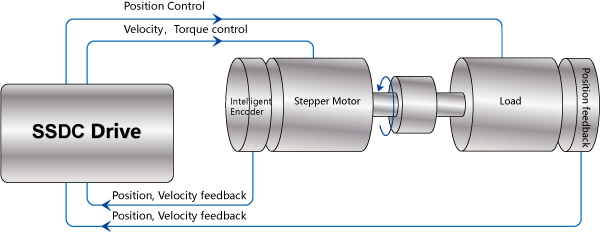
■ Safe & Convenient
• Support on-line configuration by fieldbus - Make operation more convenient
■ Low Heating / High Efficiency
• When the motor is not moving, the current can be nearly zero resulting in extremely low heat output.
• Being able to use almost 100% of the available torque allows for more efficient operation and may allow a smaller motor size.
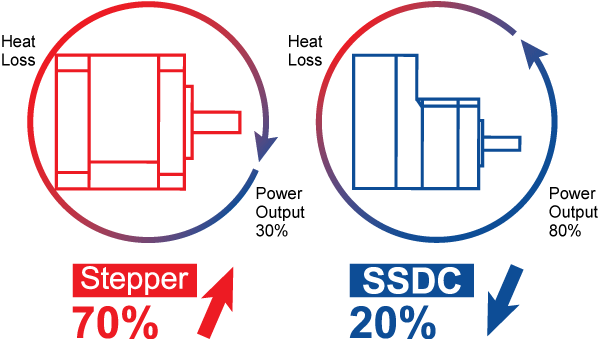
■ Smooth & Accurate
• High stiffness due to the nature of the stepper motor combined with the highly responsive servo control results in accurate position control both while running and when standing still.
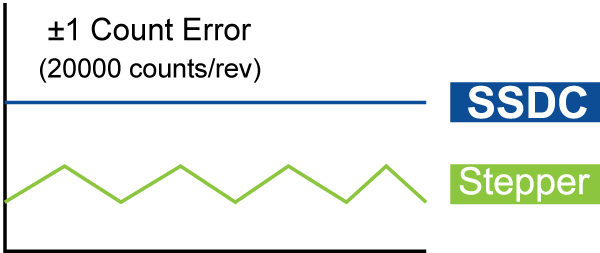
■ Fast Response
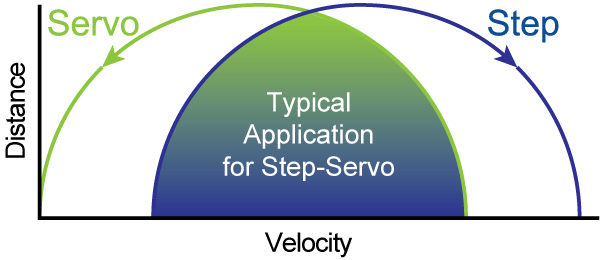
■ High Torque
• High torque capability often eliminates the need for gear reduction.
• Boost torque capability can provide as much as 50% more torque for short, quick moves.
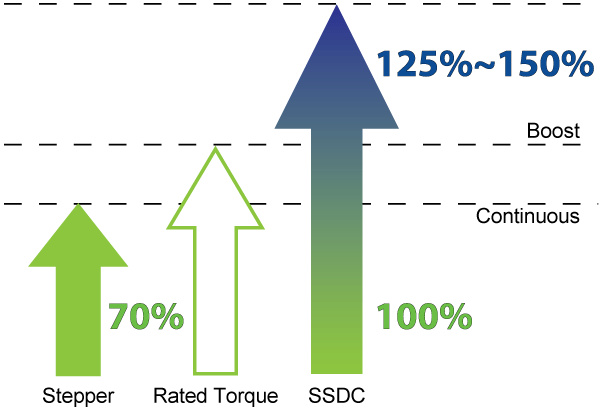
■ Motion Monitoring
• It can be used to monitor common metrics such as actual velocity and position error to assess the current actual performance of the system.
• An interactive monitoring and tuning interface provides the fastest possible performance output.
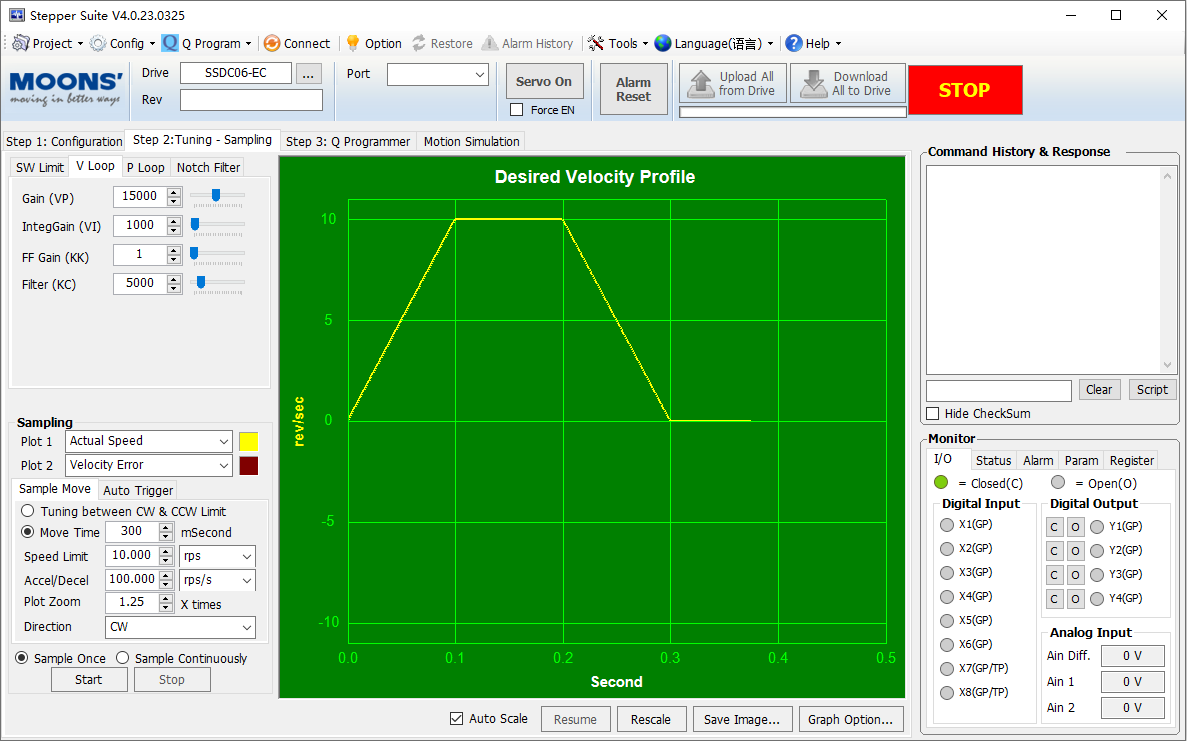
■ Easy Tuning
• A selection list provides an easy method to achieve the desired level of control.
• In most cases NO extra manual tuning is required.
• There is no need to do tuning in closed- step mode.
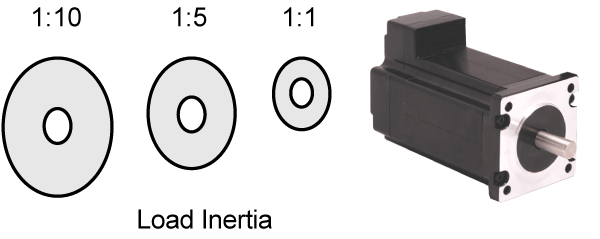
■ Software
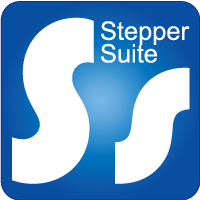
• Easy setup in just three steps
• Servo parameter tuning and sampling
• Integrated Q programming interface
• Motion Simulation and monitoring
• Write and save SCL command scripts
• Integrated online help
• Support stepper and stepper servo series products
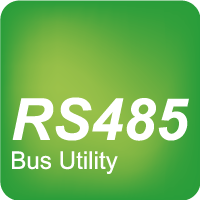
• Simple interface with powerful capability
• Easy setup with RS-485 for 32 axis network motion control
• Monitoring Status of I/O, drive, alarm and the other nine most
• Useful motion parameters
• Write and save SCL command scripts
• Online help integrated
• Supports all RS-485 drives
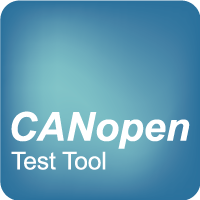
• Multiple operation Mode Support
• Multi-Thread, High Performance
• CAN bus monitor and log function
• Kvaser/PEAK adapter support
■ Software
□ Standard Series
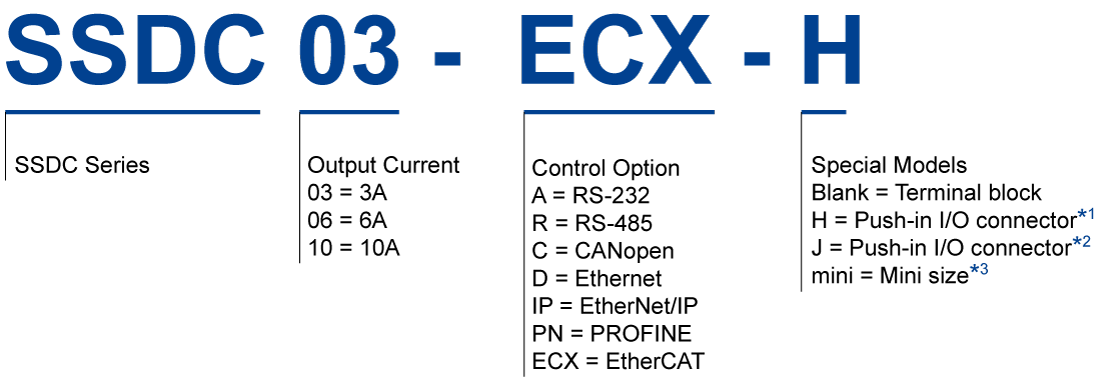
*2 :SSDC06/10-ECX-J Only
*3 :SSDC03-R-mini, SSDC06-ECX-mini Only
□ Multi-Axis Series
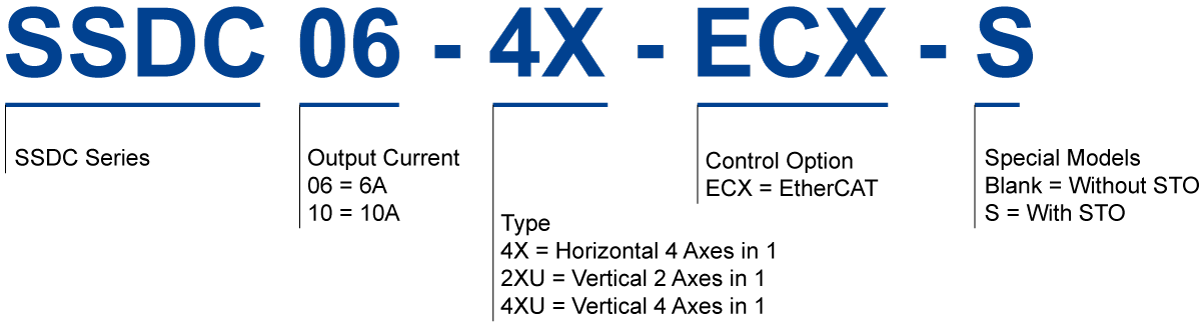
■ Ordering Information
UL | Model | Current | Voltage※ | Multi-functional Capability | ||||||||
---|---|---|---|---|---|---|---|---|---|---|---|---|
Pulse | Analog | Modbus/RTU | CANopen | Modbus/TCP | EtherNet/IP | EtherCAT | Profinet | Q Program | ||||
SSDC06-4X-ECX | 0.1-6.0A | 24-70VDC | √ | |||||||||
SSDC10-4X-ECX | 0.1-10.0A | 24-70VDC | √ | |||||||||
SSDC06-4X-ECX-S | 0.1-6.0A | 24-70VDC | √ | |||||||||
SSDC10-4X-ECX-S | 0.1-10.0A | 24-70VDC | √ | |||||||||
SSDC06-2XU-ECX | 0.1-6.0A | 24-70VDC | √ | |||||||||
SSDC10-2XU-ECX | 0.1-10.0A | 24-70VDC | √ | |||||||||
SSDC06-2XU-ECX-S | 0.1-6.0A | 24-70VDC | √ | |||||||||
SSDC10-2XU-ECX-S | 0.1-10.0A | 24-70VDC | √ | |||||||||
SSDC06-4XU-ECX | 0.1-6.0A | 24-70VDC | √ | |||||||||
SSDC10-4XU-ECX | 0.1-10.0A | 24-70VDC | √ | |||||||||
SSDC06-4XU-ECX-S | 0.1-6.0A | 24-70VDC | √ | |||||||||
SSDC10-4XU-ECX-S | 0.1-10.0A | 24-70VDC | √ | |||||||||
★ | SSDC06-ECX-H | 0.1-6.0A | 24-70VDC | √ | √ | |||||||
★ | SSDC10-ECX-H | 0.1-10.0A | 24-70VDC | √ | √ | |||||||
★ | SSDC06-ECX-J | 0.1-6.0A | 24-70VDC | √ | √ | √ | ||||||
★ | SSDC10-ECX-J | 0.1-10.0A | 24-70VDC | √ | √ | √ | ||||||
★ | SSDC06-A-H | 0.1-6.0A | 24-70VDC | √ | √ | √ | ||||||
★ | SSDC10-A-H | 0.1-10.0A | 24-70VDC | √ | √ | √ | ||||||
★ | SSDC06-PN-01 | 0.1-6.0A | 24-70VDC | √ | √ | √ | ||||||
★ | SSDC10-PN-01 | 0.1-10.0A | 24-70VDC | √ | √ | √ | ||||||
SSDC03-R-mini | 0.1-3.0A | 12-48VDC | √ | √ | ||||||||
SSDC06-ECX-mini | 0.1-6.0A | 24-48VDC | √ | √ | ||||||||
★ | SSDC03-A | 0.1-3.0A | 12-48VDC | √ | √ | √ | ||||||
★ | SSDC06-A | 0.1-6.0A | 24-70VDC | √ | √ | √ | ||||||
★ | SSDC10-A | 0.1-10.0A | 24-70VDC | √ | √ | √ | ||||||
★ | SSDC03-R | 0.1-3.0A | 12-48VDC | √ | √ | √ | √ | |||||
★ | SSDC06-R | 0.1-6.0A | 24-70VDC | √ | √ | √ | √ | |||||
★ | SSDC10-R | 0.1-10.0A | 24-70VDC | √ | √ | √ | √ | |||||
★ | SSDC03-C | 0.1-3.0A | 12-48VDC | √ | √ | |||||||
★ | SSDC06-C | 0.1-6.0A | 24-70VDC | √ | √ | |||||||
★ | SSDC10-C | 0.1-10.0A | 24-70VDC | √ | √ | |||||||
★ | SSDC03-D | 0.1-3.0A | 12-48VDC | √ | √ | √ | √ | |||||
★ | SSDC06-D | 0.1-6.0A | 24-70VDC | √ | √ | √ | √ | |||||
★ | SSDC10-D | 0.1-10.0A | 24-70VDC | √ | √ | √ | √ | |||||
★ | SSDC03-IP | 0.1-3.0A | 12-48VDC | √ | √ | √ | √ | √ | ||||
★ | SSDC06-IP | 0.1-6.0A | 24-70VDC | √ | √ | √ | √ | √ | ||||
★ | SSDC10-IP | 0.1-10.0A | 24-70VDC | √ | √ | √ | √ | √ |
★:UL certified models.
■ Driver Specifications
□ Specifications
Driver | SSDC03 | SSDC06 | SSDC10 |
---|---|---|---|
Input Voltage | 12-48VDC | 24-70VDC | 24-70VDC |
Output Current | continuous 3A, boost 4A(1.5s) | continuous 6A, boost 7.5A(1.5s) | continuous 10A, boost 15A(1.5s) |
Protection | Over-voltage, under-voltage, over-temp, motor/winding shorts (phase-to-phase, phase-to-ground) | ||
Speed Range | Up to 3000rpm | ||
Filters | Digital input noise filter, Analog input noise filter, Smoothing filter, PID filter, Notch filter | ||
Non-Volatile Storage | Configurations are saved in FLASH memory on-board the DSP | ||
Ambient Temperature | 0 to 40°C (32 to 104°F) when mounted to a suitable heatsink | ||
Ambient Humidity | 90% Max., non-condensing | ||
Mass | 0.25kg | ||
Encoder Resolution | 20000 counts/rev( for AM17/23/24/34SS-N motors) 4096 counts/rev( for AM08/11/17/23/24/34RS motors) |
□ Technical specifications
Type | EtherCAT | ||||||
---|---|---|---|---|---|---|---|
Driver | SSDC-4X-ECX | SSDC-4X-ECX-S | SSDC-2XU-ECX | SSDC-4XU-ECX | SSDC-ECX-mini | SSDC-ECX-H | SSDC-ECX-J |
Digital Inputs | 5DI*4 | 5DI*4 | 3DI*2 | 3DI*4 | 5DI | 3DI | 5DI |
Digital Outputs | 3DO*4 | 3DO*4 | 2DO*2 | 2DO*4 | 2DO | 1DO | 2DO |
Analog Inputs | NO | NO | NO | NO | NO | NO | 1 analog inputs |
Encoder Outputs | NO | NO | NO | NO | NO | NO | NO |
+5V Output | NO | NO | NO | NO | NO | NO | 5VDC,100mA |
Bus Control | EtherCAT | EtherCAT | EtherCAT | EtherCAT | EtherCAT | EtherCAT | EtherCAT |
Counts/IO | NO | NO | NO | NO | NO | NO | NO |
PLC(Q programmer) | NO | NO | NO | NO | YES | YES | YES |
Type | RS485 | RS232 | CANopen | Ethernet | ||||
---|---|---|---|---|---|---|---|---|
Driver | SSDC**-R-mini | SSDC**-R | SSDC**-A | SSDC**-A-H | SSDC**-C | SSDC**-D | SSDC**-IP | SSDC**-PN |
Digital Inputs | 2DI | 8DI | 8DI | 4DI | 8DI | 8DI | 8DI | 8DI |
Digital Outputs | 1DO | 4DO | 4DO | 3DO | 4DO | 4DO | 4DO | 4DO |
Analog Inputs | NO | 2 analog inputs | 2 analog inputs | NO | 2 analog inputs | 2 analog inputs | 2 analog inputs | 2 analog inputs |
Encoder Outputs | NO | ABZ differential | ABZ differential | NO | ABZ differential | ABZ differential | ABZ differential | ABZ differential |
+5V Output | NO | 5VDC,100mA | 5VDC,100mA | NO | 5VDC,100mA | 5VDC,100mA | 5VDC,100mA | 5VDC,100mA |
Bus Control | Modbus/RTU SCL | Modbus/RTU SCL | SCL | SCL | CANopen | Modbus/TCP eSCL | Profinet Modbus/TCP eSCL | Ethernet/IP Modbus/TCP eSCL |
Counts/IO | NO | YES | YES | YES | YES | YES | YES | YES |
PLC(Q programmer) | YES | YES | YES | YES | NO | YES | YES | YES |
■ Recommended Motors
Model | Drive P/N | Torque | Rotor Inertia | Encoder Resolution | Maximum Speed | Mass | Frame Size | Permissible Overhung Load(N) | Permissible Thrus Load | ||||
---|---|---|---|---|---|---|---|---|---|---|---|---|---|
Nm | gcm2 | counts/rev | RPM | g | mm | Distance(L) from Shaft End(mm) | |||||||
AM11RS1DMA | SSDC03 | 0.065 | 9 | 4096 | 3600 | 118 | 28 | 20 | 25 | 34 | 52 | - | Less than the motor mass |
AM11RS2DMA | 0.08 | 12 | 168 | ||||||||||
AM11RS3DMA | 0.125 | 18 | 218 | ||||||||||
AM17RS1DM □ | SSDC03 or SSDC06 | 0.26 | 38 | 4096 | 3600 | 390 | 42 | 35 | 44 | 58 | 85 | - | |
AM17RS2DM □ | 0.42 | 57 | 440 | ||||||||||
AM17RS3DM □ | 0.52 | 82 | 520 | ||||||||||
AM17RS4DM □ | 0.7 | 123 | 760 | ||||||||||
AM17SS1DG □ -N | 0.26 | 38 | 20000 | 3600 | 390 | ||||||||
AM17SS2DG □ -N | 0.42 | 57 | 440 | ||||||||||
AM17SS3DG □ -N | 0.52 | 82 | 520 | ||||||||||
AM17SS4DG □ -N | 0.7 | 123 | 760 | ||||||||||
AM23RS2DM □ | SSDC06 or SSDC10 | 0.95 | 260 | 4096 | 3600 | 850 | 56 | 63 | 75 | 95 | 130 | 190 | |
AM23RS3DM □ | 1.5 | 460 | 1250 | ||||||||||
AM23RS4DMA | 2.4 | 365 | 1090 | ||||||||||
AM23SS2DG □ -N | 0.95 | 260 | 20000 | 3600 | 850 | ||||||||
AM23SS3DG □ -N | 1.5 | 460 | 1250 | ||||||||||
AM23SS4DGA-N | 2.4 | 365 | 1090 | ||||||||||
AM24RS3DM □ | 2.5 | 900 | 4096 | 3600 | 1650 | 60 | 90 | 100 | 130 | 180 | 270 | ||
AM24SS3DG □ -N | 2.5 | 900 | 20000 | 3600 | 1650 | ||||||||
AM34RS1DMA | SSDC10 | 2.7 | 915 | 4096 | 3600 | 2000 | 86 | 260 | 290 | 340 | 390 | 480 | |
AM34RS3DMA | 5.2 | 1480 | 3100 | ||||||||||
AM34RS5DMA | 7.0 | 2200 | 4200 | ||||||||||
AM34SS1DGA-N | 2.7 | 915 | 20000 | 3600 | 2000 | ||||||||
AM34SS3DGA-N | 5.2 | 1480 | 3100 | ||||||||||
AM34SS5DGA-N | 7.0 | 2200 | 4200 | ||||||||||
口:A 或B,详见电机命名规则 |
■ Driver Dimensions (Unit:mm)
■ Motor Dimensions (Unit:mm)
Model | L |
---|---|
AM08RS1DMA | 45.5 |
AM08RS2DMA | 55.5 |
AM08RS3DMA | 62.5 |
Model | L |
---|---|
AM11RS1DMA | 43.8 |
AM11RS2DMA | 52.9 |
AM11RS3DMA | 64.1 |
Model | A | A1 | B | B1 | L |
---|---|---|---|---|---|
AM17RS1DMA | φ6 | 5.5 | 20 | 15 | 59.5 |
AM17RS1DMB | φ5 | 4.5 | 24 | 15 | 59.5 |
AM17RS2DMA | φ6 | 5.5 | 20 | 15 | 65 |
AM17RS2DMB | φ5 | 4.5 | 24 | 15 | 65 |
AM17RS3DMA | φ6 | 5.5 | 20 | 15 | 73.5 |
AM17RS3DMB | φ5 | 4.5 | 24 | 15 | 73.5 |
AM17RS4DMA | φ6 | 5.5 | 20 | 15 | 89 |
AM17RS4DMB | φ5 | 4.5 | 24 | 15 | 89 |
AM17SS1DGA-N | φ6 | 5.5 | 20 | 15 | 59.5 |
AM17SS1DGB-N | φ5 | 4.5 | 24 | 15 | 59.5 |
AM17SS2DGA-N | φ6 | 5.5 | 20 | 15 | 65 |
AM17SS2DGB-N | φ5 | 4.5 | 24 | 15 | 65 |
AM17SS3DGA-N | φ6 | 5.5 | 20 | 15 | 73.5 |
AM17SS3DGB-N | φ5 | 4.5 | 24 | 15 | 73.5 |
AM17SS4DGA-N | φ6 | 5.5 | 20 | 15 | 89 |
AM17SS4DGB-N | φ5 | 4.5 | 24 | 15 | 89 |
Model | A | A1 | B | B1 | L |
---|---|---|---|---|---|
AM23RS2DMA | φ8 | 7.5 | 24 | 20 | 77.5 |
AM23RS2DMB | φ6.35 | 5.85 | 20 | 15 | 77.5 |
AM23RS3DMA | φ8 | 7.5 | 24 | 20 | 99.5 |
AM23RS3DMB | φ6.35 | 5.85 | 20 | 15 | 99.5 |
AM23RS4DMA | φ8 | 7.5 | 24 | 20 | 102.5 |
AM23SS2DGA-N | φ8 | 7.5 | 24 | 20 | 77.5 |
AM23SS2DGB-N | φ6.35 | 5.85 | 20 | 15 | 77.5 |
AM23SS3DGA-N | φ8 | 7.5 | 24 | 20 | 99.5 |
AM23SS3DGB-N | φ6.35 | 5.85 | 20 | 15 | 99.5 |
AM23SS4DGA-N | φ8 | 7.5 | 24 | 20 | 102.5 |
Model | A | A1 | B | B1 |
---|---|---|---|---|
AM24RS3DMA | φ10 | 9.5 | 24 | 20 |
AM24RS3DMB | φ8 | 7.5 | 20.6 | 15 |
AM24SS3DGA-N | φ10 | 9.5 | 24 | 20 |
AM24SS3DGB-N | φ8 | 7.5 | 20.6 | 15 |
Model | L |
---|---|
AM34RS1DMA | 88 |
AM34RS3DMA | 117.5 |
AM34RS5DMA | 147 |
AM34SS1DGA-N | 88 |
AM34SS3DGA-N | 117.5 |
AM34SS5DGA-N | 147 |
■ With Brake Motor Dimensions (Unit:mm)
Model | A | A1 | B | L |
---|---|---|---|---|
AM17SS1DGA-N-BR01 | φ6 | 5.5 | 20 | 59.5 |
AM17SS1DGB-N-BR01 | φ5 | 4.5 | 24 | 59.5 |
AM17SS2DGA-N-BR01 | φ6 | 5.5 | 20 | 65 |
AM17SS2DGB-N-BR01 | φ5 | 4.5 | 24 | 65 |
AM17SS3DGA-N-BR01 | φ6 | 5.5 | 20 | 73.5 |
AM17SS3DGB-N-BR01 | φ5 | 4.5 | 24 | 73.5 |
AM17SS4DGA-N-BR01 | φ6 | 5.5 | 20 | 89 |
AM17SS4DGB-N-BR01 | φ5 | 4.5 | 24 | 89 |
Model | Voltage (VDC) | Torque (N.m) | Power (W) | Reactive time (ms) | Life (times) | Maximum speed (rpm) | Insulation class |
---|---|---|---|---|---|---|---|
NEMA17 Brake | 24 | 0.6 | 5 | 50 | 10000 | 5000 | Class B |
Model | A | A1 | B | B1 | L |
---|---|---|---|---|---|
AM23SS2DGA-N-BR01 | φ8 | 7.5 | 24 | 20 | 77.5 |
AM23SS2DGB-N-BR01 | φ6.35 | 5.85 | 20 | 15 | 77.5 |
AM23SS3DGA-N-BR01 | φ8 | 7.5 | 24 | 20 | 99.5 |
AM23SS3DGB-N-BR01 | φ6.35 | 5.85 | 20 | 15 | 99.5 |
AM23SS4DGA-N-BR01 | φ8 | 7.5 | 24 | 20 | 102.5 |
Model | Voltage (VDC) | Torque (N.m) | Power (W) | Reactive time (ms) | Life (times) | Maximum speed (rpm) | Insulation class |
---|---|---|---|---|---|---|---|
NEMA23 Brake | 24 | 1.2 | 4.5 | 50 | 10000 | 5000 | Class B |
Model | A | A1 | B | B1 |
---|---|---|---|---|
AM24SS3DGA-N-BR01 | φ10 | 9.5 | 24 | 20 |
AM24SS3DGB-N-BR01 | φ8 | 7.5 | 20.6 | 15 |
Model | Voltage (VDC) | Torque (N.m) | Power (W) | Reactive time (ms) | Life (times) | Maximum speed (rpm) | Insulation class |
---|---|---|---|---|---|---|---|
NEMA24 Brake | 24 | 1.2 | 4.5 | 50 | 10000 | 5000 | Class B |
Model | L |
---|---|
AM34SS1DGA-N-BR01 | 88 |
AM34SS3DGA-N-BR01 | 117.5 |
AM34SS5DGA-N-BR01 | 147 |
Model | Voltage (VDC) | Torque (N.m) | Power (W) | Reactive time (ms) | Life (times) | Maximum speed (rpm) | Insulation class |
---|---|---|---|---|---|---|---|
NEMA34 Brake | 24 | 6.0 | 8.0 | 50 | 10000 | 5000 | Class B |
Title | Type | Size(KB) | Download |
---|---|---|---|
SSDC03-R-mini Quick Setup Guide_EN20240325.pdf | 514 |
Title | Type | Size(KB) | Download |
---|---|---|---|
SSDC Family Brochure_EN20240513_A8L.pdf | 3571 |
Title | Type | Size(KB) | Download |
---|---|---|---|
Modbus RTU Manual_EN20171018.pdf | 1470 | ||
SSDC-D/IP Hardware Manual_EN20210527.pdf | 5966 | ||
SSDC-R/C Hardware Manual_EN20210527.pdf | 6718 | ||
EtherCAT UserManual EN20210427.pdf | 2260 | ||
HOST COMMAND reference uesr manual.pdf | 6963 | ||
SSDC-EC Hardware Manual_EN20210528.pdf | 6613 | ||
SSDC-A Hardware Manual_EN20210528.pdf | 5475 | ||
CANopen UserManual_EN20210816.pdf | 1238 | ||
SSDC-ECX-H/J Hardware Manual_EN20230217.pdf | 5307 | ||
SSDC-Multi Axis Series Hardware Manual_EN20231215.pdf | 4791 | ||
EtherCAT Multi Axis UserManual EN20250311.pdf | 2162 |
Title | Type | Size(KB) | Download |
---|---|---|---|
ROHS declaration-2024-A0.pdf | 522 | ||
UL Certification for SSDC&STF Series Stepper Drives.pdf | 301 | ||
UKCA Certification for SSDC.pdf | 1613 | ||
CE Certification for SSDC&STF Multi-Axis Series .pdf | 1662 |
Title | Type | Size(KB) | Download |
---|---|---|---|
Stepper Suite Setup 4.0.24.1225.zip | ZIP | 22841 | |
Step-Servo Quick Tuner Setup 3.0.19.0109.zip | ZIP | 37231 | |
RS485 Bus Utility Setup 1.0.18.0510.rar | RAR | 1898 | |
CANopen Test Tool Setup 1.0.23.0506.zip | ZIP | 10024 | |
AMA Step-Servo EtherCAT v3.2.6.zip | XML | 156 | |
SSDC-IP EDS.rar | RAR | 30 | |
AMA MultiAxes StepServo EtherCAT v1.1.3.zip | XML | 24 | |
CAN_EDS V310B_SSDC.eds | EDS | 45 |
Filter By Product Type
All ProductsExtended Encoder Cables
Extended I/O Cables
Extended Motor Cables
USB Cable
Communiaction Cables
Motor Types
Regen Clamp
RS485 Adapter

Delivery & Packaging
Ensure your ordered products are always safely packaged from easy click to fast delivery to your handsProfessional Product Label
Considering all possible harsh application environments, MOONS' specially designed labels for each product, which pass water-resistance test, durability rub test, high temperature resistance and corrosion resistance tests.Besides, our product labels are attached with QR code linking to product details, which is convenient for clients to view the detail product page with their mobile phones.
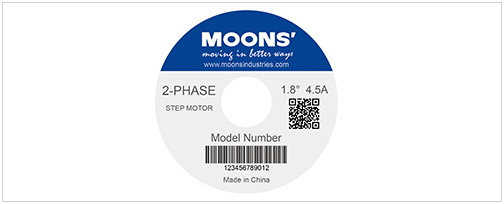
Note: This label design is suitable for products of stepper motor.
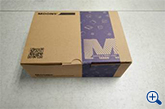
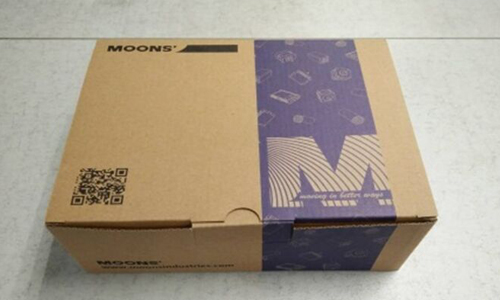
(Professional packing box and unique appearance design)
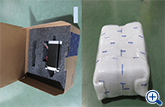
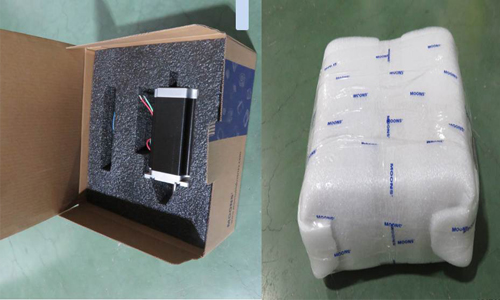
(Single item packed with EPE)
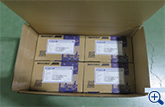
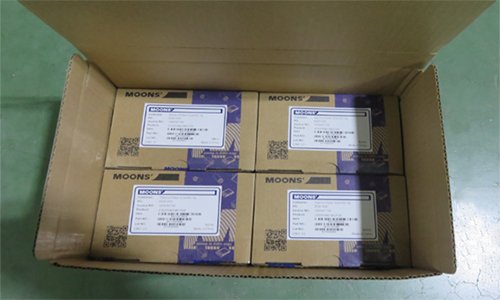
(Multi-products packed with another box)
Safely Packaging
In order to ensure your shipments withstand the long trip and arrive safely and intact, MOONS' specially designed Individual package to pass the drop test with its stable structure.Besides,the package is made from recyclable materials, providing you with professional safety delivery.
Whether just single item or multi-products the clients buy, all products are packed twice to avoid the damage further.
Shipping Visualization
For each case, products are carefully packed by experienced warehouse staff and the key processes are recorded by photos, which are then posted on our website, so that clients could clearly know the packing process and logistics status after placing order.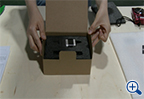
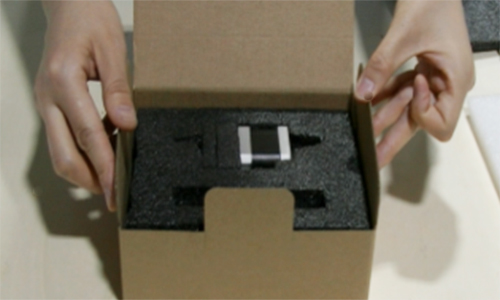
(Product in the box)
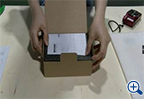
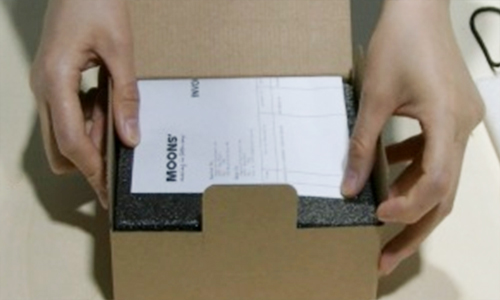
(Add the invoice)
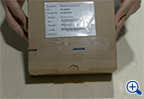
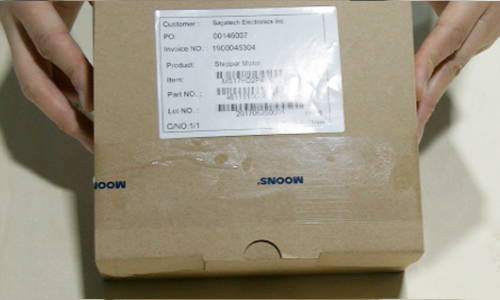
(Label the commodity)
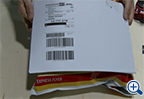
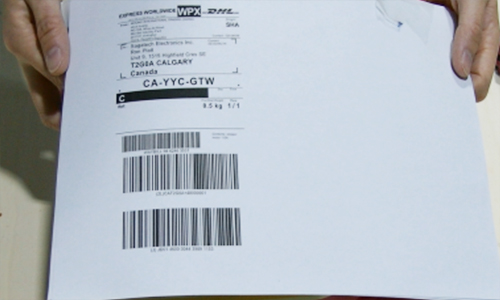
(The logistics waybill attached)
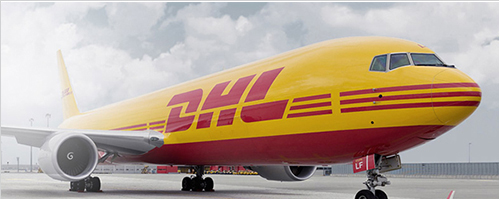
Fast Delivery
Fast Cross-Border DeliveryMOONS' chooses DHL as our main international express shipping partner. As the world's leading logistics specialist, DHL provides our customers with fast and professional inter- national door-to-door delivery service.
Estimated Delivery Time: e.g. China-USA major cities 3 business days.
Professional
Warehouse Management
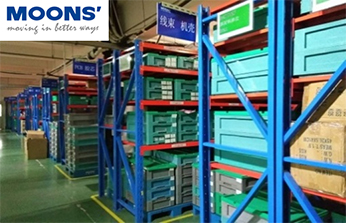