* Free shipping to North America and most of Europe for orders of $100 or more
ID M56S Series High-End AC Input Servo Drives
M56S series is a new generation of high-end 220V/400V AC input servo system, the power range is from 50W to 7.5KW. The drive adopts advanced motion control algorithms, coupled with a 26-bit high precision encoder motor, the velocity loop bandwidth is up to 3.5KHz. Efficient automatically adjusts the loop gain, superior vibration suppression and external disturbance compensation performance. The drive supports full closed-loop control, built-in regenerative energy absorption resistor, STO safety function and dynamic braking module (for certain models). It supports the control mode of position, velocity, torque and Q programming. EtherCAT, CANopen, Modbus, EtherNet/IP, and Profinet industrial fieldbus are available.● Better vibration suppression and external disturbance compensation performance
● Power range of 50W to 7.5kW
● Full closed-loop, STO function safety
● Velocity loop bandwidth up to 3.5kHz
● Built-in dynamic braking function
● Efficient auto-tuning
● CE, UL, STO (SIL 3) certification
● Supports EtherCAT, CANopen, Modbus, EtherNet/IP, Profinet field bus



- current tab: Description & Feature
- Data Sheet
- Online Ordering
- Downloads
- Recommended Options
- Delivery & Packaging
Features |
---|
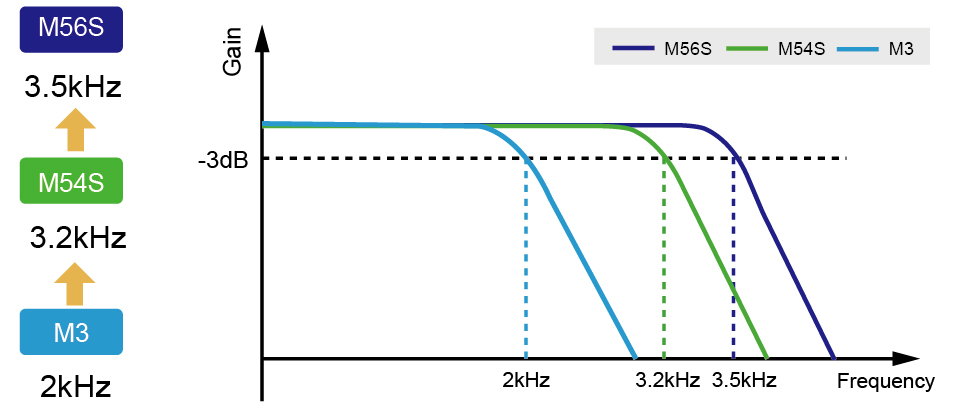
26-bit Multi-turn Absolute Optical Encoder
◆ High resolution, up to 67,108,864 divisions per revolution
◆ Optional battery backup for 16-bit multi-turn
21-bit Multi-turn Absolute Magnetic Encoder
◆ High resolution, up to 2,097,152 divisions per revolution
◆ Optional battery backup for 16-bit multi-turn
◆ Strong vibration resistance
◆ Resistant to dust and oil stains
◆ Anti condensation
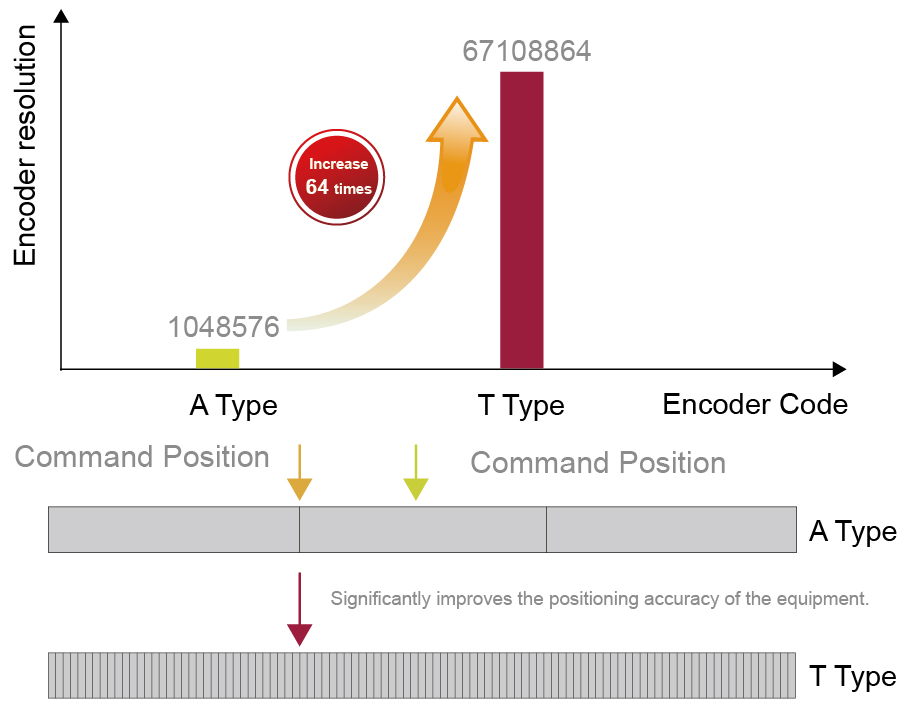
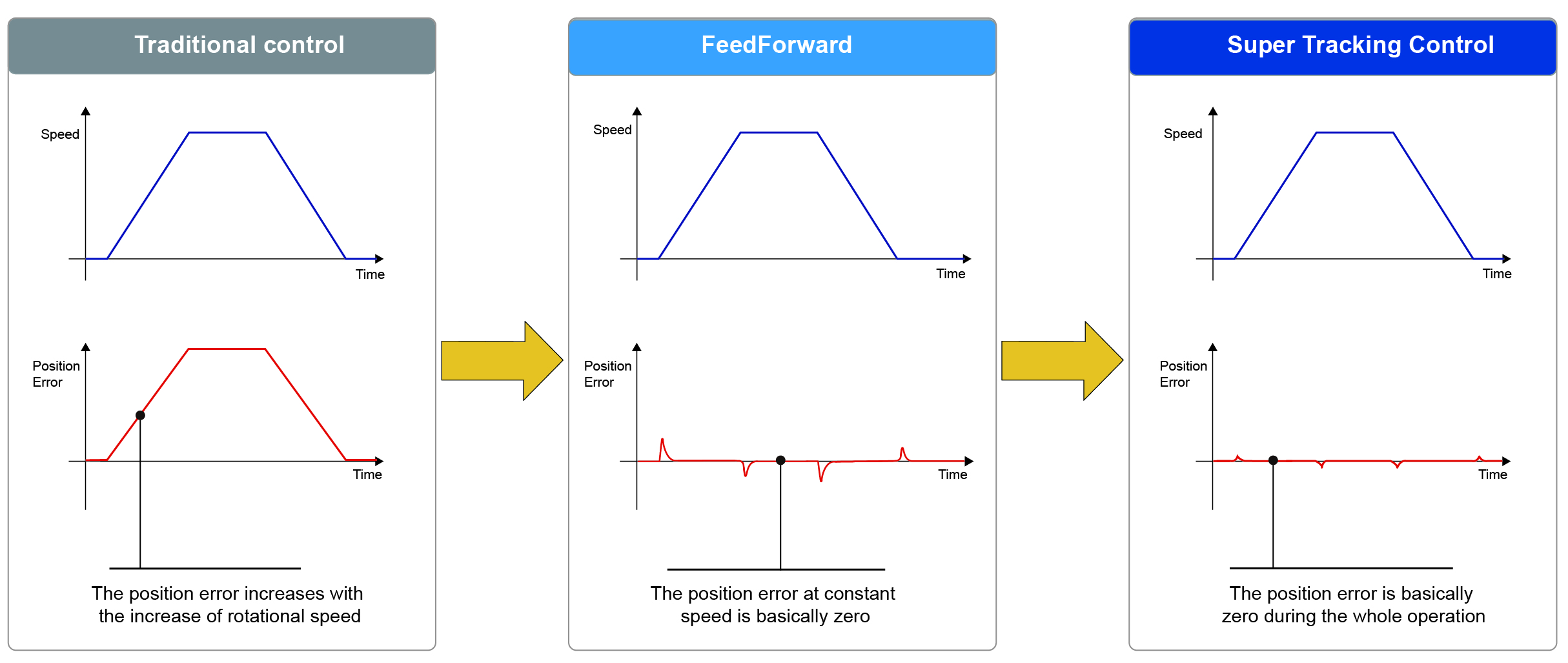
◆ No limitation towards any load type and drive control mode.
◆ High robustness for maximum control of servo system stability.
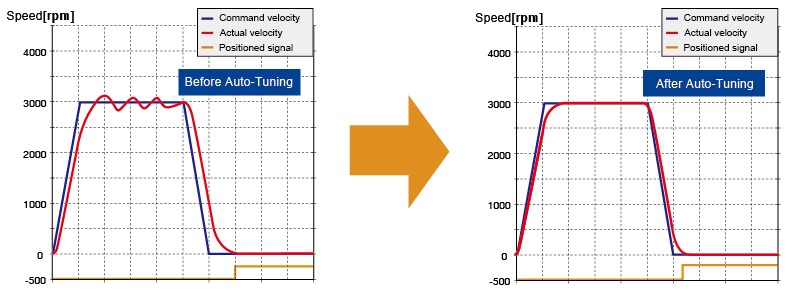
For example, the accuracy of arc trajectory in the interpolation control of XY mechanism can be improved.
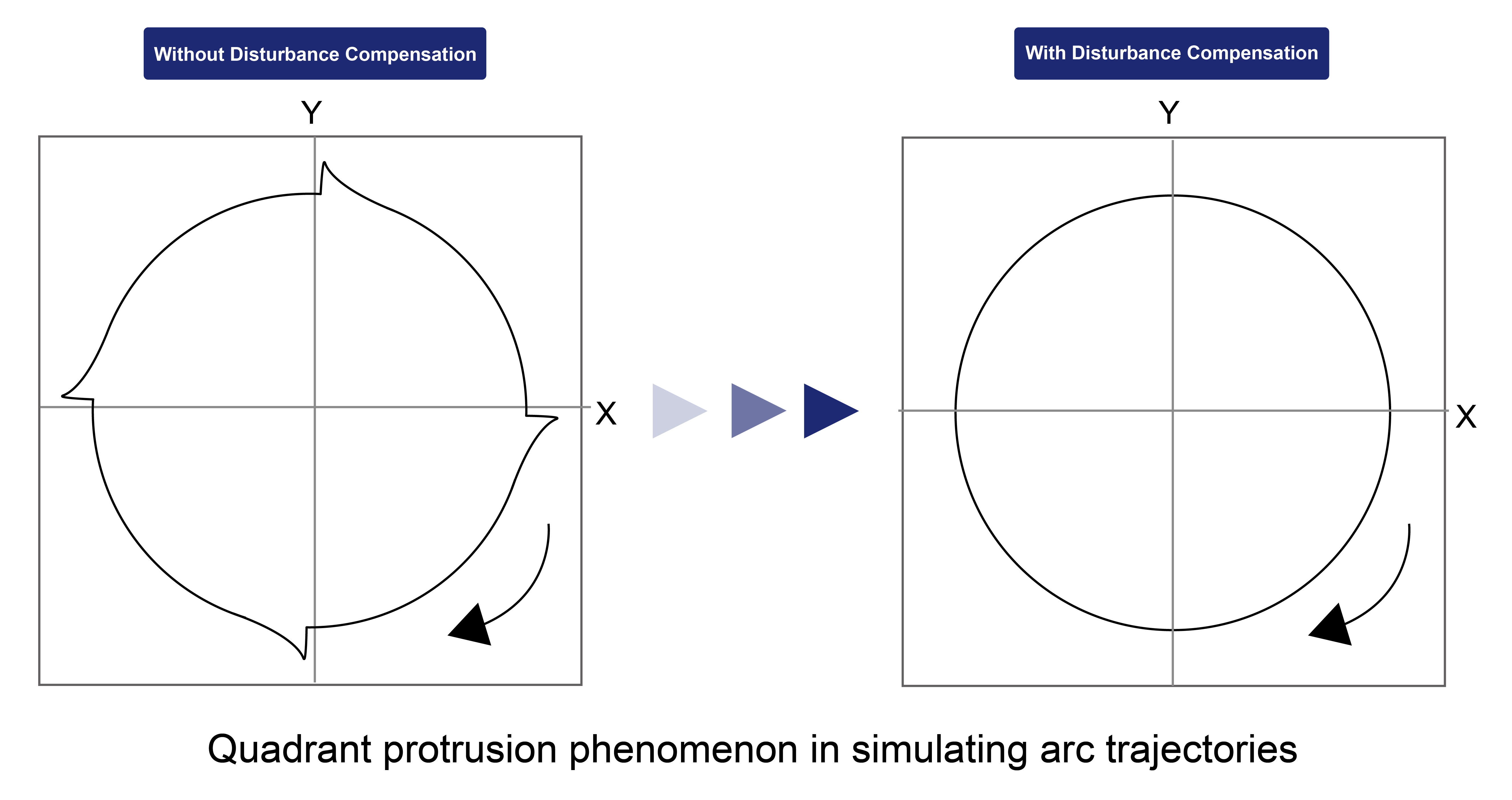
◆ 2 sets of automatically set notch filters can search and set resonance frequency automatically.
◆ 2 sets of manual notch filters for more adjust options.
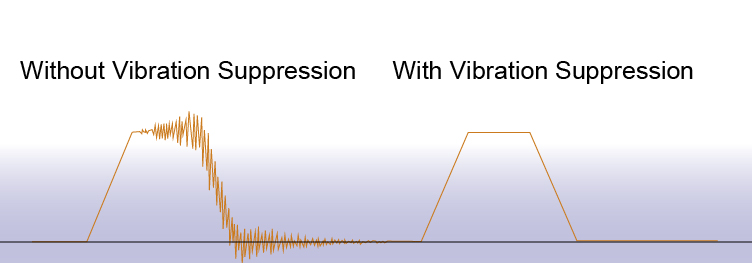
Novel Resonance Suppression The new resonance suppression function of the M56S series products can effectively suppress the low-frequency vibration caused by the resonance of 100 ~ 1000Hz. | Mechanical End Vibration Suppression Vibration at the end of the machine will lead to longer system settling time, resulting in decreased machine precision or production efficiency. M56S servo can suppress vibrations at the end of the machine, shortening tuning time, increasing the system precision and productivity. | |
![]() | ![]() |
M56S series drive meets UL61800-5-2(SIL 3),IEC61508(SIL 3),ISO138491(PL e).
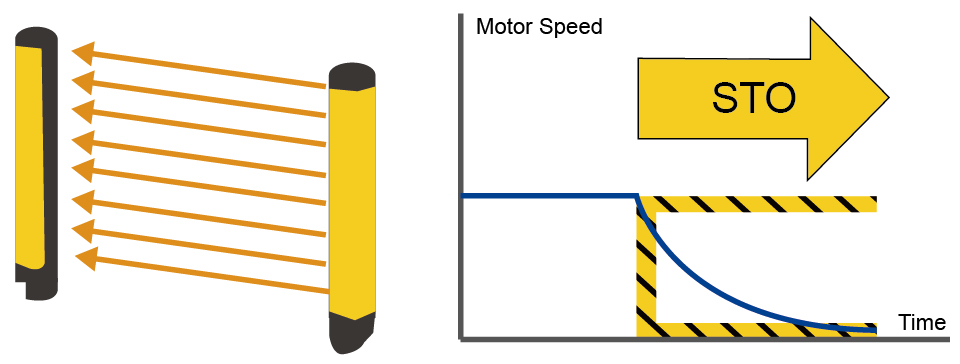
Without Dynamic brake | With Dynamic brake | |
![]() | ![]() | |
In this scenario, the drive exhibits a fault and is disabled. This results in the motor coming to an uncontrolled deceleration that is influenced purely by external factors such as the speed of the motor before fault, inertia of the system and the friction present in the system. | In this scenario, the drive exhibits a fault and is disabled. The phases (U/V/W) of the servo motor are shorted and the current generated by the back EMF of the motor windings is used to stop the motor. This greatly reduces deceleration time and protects personnel as well as equipment. |
Built-in Regenerative Absorbing Resistor Almost all the M56S drives have built-in regenerative absorbing resistor, it can consume the regenerative energy generated when the motor and load decelerate rapidly, make sure the servo system can stop quickly and operate reliably.No additional regen resistor is required for most applications. | Main Power Power-off & Phase Loss Detection The M56S servo drives monitor main power and motor phase connections. Should either of these be lost, a fault will occur. This serves as an added protection measure against damage that might result from these issues. | |
![]() | ![]() |
Drive Part Numbering |
---|
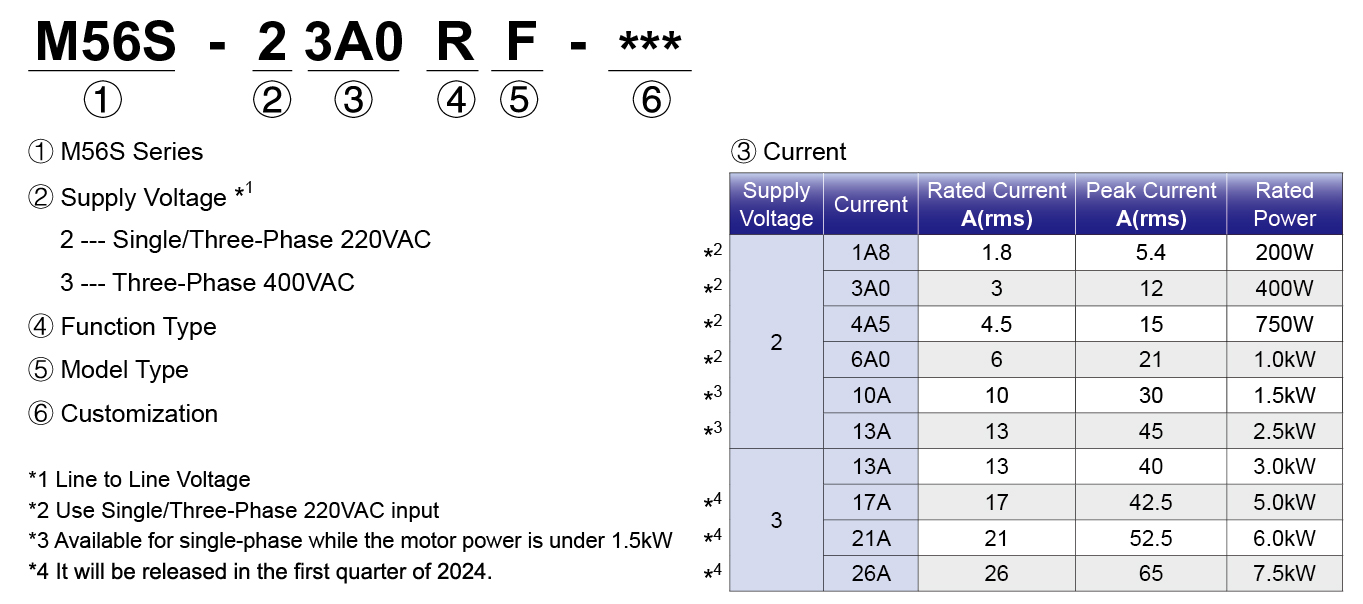
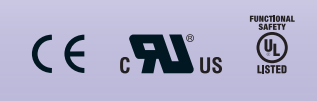
■ Drive Specification –R: RS-485 Type 220VAC
Input Power | M56S-21A8 ■◆ M56S-23A0 ■◆ M56S-24A5 ■◆ M56S-26A0RF | Main Circuit | Single / Three-phase, AC200 ~ 240V ±10%,50/60Hz |
---|---|---|---|
Control Circuit | Single-phase, AC200 ~ 240V ±10%,50/60Hz | ||
M56S-210ARF M56S-213ARF | Main Circuit | Three-phase, AC200 ~ 240V ±10%,50/60Hz | |
Control Circuit | Single-phase, AC200 ~ 240V ±10%,50/60Hz | ||
Withstand Voltage | Primary to earth: withstand 1500 VAC, 1 min, (Leakage current: 20 mA) [220V Input] | ||
Environment | Temperature | Ambient temperature: 0°C ~ 55°C (If the ambient temperature of servo drive is higher than 45°C, please install the drive in a well-ventilated location) | |
Humidity | Both operating and storage : 10 ~ 85%RH or less | ||
Altitude | Derating is not required for altitudes not higher than 1000m Derating 1% for every additional 100m for altitudes between 1000m and 2000m | ||
Vibration | 9.8m/s2 or less, 10 ~ 60Hz (Do not use continuously at resonance frequency) | ||
Motor Encoder Feedback | ● 26-bit Multi-turn Absolute Optical Encoder ● 21-bit Multi-turn Absolute Magnetic Encoder ● 17-bit Battery-less Multi-turn Absolute Encoder | ||
Second Encoder Feedback* *1 | A/B/Z phase signal differential input | ||
I/O | Digital Signal | Input | 10 Configurable optically isolate digital general inputs, 24VDC, 20mA |
Output | 6 Configurable optically isolate digital general outputs, Max. 30VDC,100mA | ||
Analog Signal | Input | 2 Analog inputs, -10 ~ +10V, 12bit | |
Output*2 | 2 Analog outputs, -10 ~ +10V, Max.10mA | ||
Pulse Signal | Input | 2 Pulse Inputs (Optocoupler input, Line Receiver input): ● Optocoupler input: 5 ~ 24V, minimum pulse width 1μs, max. pulse frequency 500KHz ● Line Receiver input: 5V differential signal, minimum pulse width 0.125μs, max. pulse frequency 4MHz | |
Output | 4 Outputs(3 Line Driver outputs, 1 open collector output) ● Line Driver output: Encoder A、B、Z feedback output ● Open collector output: Encoder Z phase | ||
Comm Port | USB | Connection with PC for configuration | |
RS-485 | Modbus/RTU Communication protocol | ||
Front Panel | 4 keys (MODE, UP, DOWN, SET) 5 - digital LED Display | ||
Regeneration Resistor | ● -F Type Built-in regenerative resistor ● -D Type 750W Built-in regenerative resistor ● All models can be equipped with external absorption resistors | ||
Control Mode | 1. Pulse Position Mode 2. Analog Velocity Mode 3. Analog Torque Mode 4. Internal Position Mode 5. Internal Torque Mode 6. Internal Velocity Mode 7. Command Torque Mode 8. Full Closed Loop Control Mode*3, Each control mode can be switched by digital input | ||
Control Input Signal | Servo-ON, Alarm Reset, CW/CCW Limit, Control Mode Select, Gain Select, Clear Position Error, Zero Speed Clamp, Command and Velocity input Direction control, Command and Torque input Direction control, Emergency Stop, Homing Switch, Torque Limit, Speed Limit, Pulse Inhibit, Multi-velocity Switch, Start Q Program, General Purpose Input | ||
Control Output Signal | Warning Output, Fault Output, Servo Ready, Velocity Reached, Torque Reached, Position Reached, Servo-on Status, Brake Release, Dynamic Position Error Following, Positioning Complete, Zero Speed Detected, Velocity Coincidence, Torque Coincidence, Velocity limit, Torque limit, Homing Finished, Soft Limit CW/CCW, General Purpose Output | ||
Protection | Over Current, Over Voltage,Under Voltage, Over Temperature, Bad Encoder Feedback, Over Load, Over Speed, Positon Error, STO, CW/CCW Limit, Full Closed-loop Hybrid Deviation Fault, Main Power Phase Loss | ||
Dynamic Brake | -F Type Built in | ||
STO | -F Type Built in | ||
Weight | M56S-21A8 ■◆:0.8Kg M56S-23A0 ■◆:1.1Kg M56S-24A5 ■◆:1.6Kg M56S-26A0RF:1.9Kg M56S-210ARF:1.9Kg M56S-213ARF:1.9Kg |
■ Drive Specification -R:RS-485 Type 400VAC
Input Power | M56S-313ARF M56S-317ARF M56S-321ARF M56S-326ARF | Main Circuit | Three-phase, AC380 ~ 480V ±10%,50/60Hz |
---|---|---|---|
Control Circuit | Single-phase, AC380 ~ 480V ±10%,50/60Hz | ||
Withstand Voltage | Primary to earth: withstand 1800 VAC, 1 min, (Leakage current: 20 mA) [220V Input] | ||
Environment | Temperature | Ambient temperature: 0°C ~ 55°C (If the ambient temperature of servo drive is higher than 45°C, please install the drive in a well-ventilated location) Storage temperature: -20°C ~ 65°C | |
Humidity | Both operating and storage : 10 ~ 85%RH or less | ||
Altitude | Derating is not required for altitudes not higher than 1000m Derating 1% for every additional 100m for altitudes between 1000m and 2000m | ||
Vibration | 9.8m/s2 or less, 10 ~ 60Hz (Do not use continuously at resonance frequency) | ||
Motor Encoder Feedback | ● 23-bit Multi-turn Absolute Optical Encoder ● 21-bit Multi-turn Absolute Magnetic Encoder | ||
Second Encoder Feedback*1 | A/B/Z phase signal differential input | ||
I/O | Digital Signal | Input | 10 Configurable optically isolate digital general inputs, 24VDC, 20mA |
Output | 6 Configurable optically isolate digital general outputs, Max. 30VDC,100mA | ||
Analog Signal | Input | 2 Analog inputs, -10 ~ +10V, 12bit | |
Output*2 | 2 Analog outputs, -10 ~ +10V, Max.10mA | ||
Pulse Signal | Input | 2 Pulse Inputs (Optocoupler input, Line Receiver input): ● Optocoupler input: 5 ~ 24V, minimum pulse width 1μs, max. pulse frequency 500KHz ● Line Receiver input: 5V differential signal, minimum pulse width 0.125μs, max. pulse frequency 4MHz | |
Output | 4 Outputs(3 Line Driver outputs, 1 open collector output) ● Line Driver output: Encoder A、B、Z feedback output ● Open collector output: Encoder Z phase | ||
Comm Port | USB | Connection with PC for configuration | |
RS-485 | Modbus/RTU Communication protocol | ||
Front Panel | 4 keys (MODE, UP, DOWN, SET) 5 - digital LED Display | ||
Regeneration Resistor | Built-in regenerative resistor (All models can be equipped with external absorption resistors) | ||
Control Mode | 1. Pulse Position Mode 2. Analog Velocity Mode 3. Analog Torque Mode 4. Internal Position Mode 5. Internal Torque Mode 6. Internal Velocity Mode 7. Command Torque Mode 8. Full Closed Loop Control Mode*3, Each control mode can be switched by digital input | ||
Control Input Signal | Servo-ON, Alarm Reset, CW/CCW Limit, Control Mode Select, Gain Select, Clear Position Error, Zero Speed Clamp, Command and Velocity input Direction control, Command and Torque input Direction control, Emergency Stop, Homing Switch, Torque Limit, Speed Limit, Pulse Inhibit, Multi-velocity Switch, Start Q Program, General Purpose Input | ||
Control Output Signal | Warning Output, Fault Output, Servo Ready, Velocity Reached, Torque Reached, Position | ||
Protection | Over Current, Over Voltage,Under Voltage, Over Temperature, Bad Encoder Feedback, Over | ||
Dynamic Brake | Built in | ||
STO | Built in | ||
Weight | M56S-313ARF:1.9Kg M56S-317ARF:3.8Kg M56S-321ARF:3.8Kg M56S-326ARF:3.8Kg |
■ Drive Specification -EC—EtherCAT Type -C—CANopenType 220VAC
Input Power | M56S-21A8 ■◆ M56S-23A0 ■◆ M56S-24A5 ■◆ M56S-26A0 ■ X | Main Circuit | Single / Three-phase,AC200 ~ 240V ±10%,50/60Hz |
---|---|---|---|
Control Circuit | Single-phase,AC200 ~ 240V ±10%,50/60Hz | ||
M56S-210A ■ X M56S-213A ■ X | Main Circuit | Three-phase,AC200 ~ 240V ±10%,50/60Hz | |
Control Circuit | Single-phase,AC200 ~ 240V ±10%,50/60Hz | ||
Withstand Voltage | Primary to earth: withstand 1500 VAC, 1 min, (Leakage current: 20 mA) [220V Input] | ||
Environment | Temperature | Ambient temperature: 0°C ~ 55°C (If the ambient temperature of servo drive is higher Storage temperature: -20°C ~ 65°C | |
Humidity | Both operating and storage : 10 ~ 85%RH or less | ||
Altitude | Derating is not required for altitudes not higher than 1000m Derating 1% for every additional 100m for altitudes between 1000m and 2000m | ||
Vibration | 9.8m/s2 or less, 10 ~ 60Hz (Do not use continuously at resonance frequency) | ||
Motor Encoder Feedback | ● 26-bit Multi-turn Absolute Optical Encoder ● 21-bit Multi-turn Absolute Magnetic Encoder ● 17-bit Battery-less Multi-turn Absolute Encoder | ||
Second Encoder Feedback*1 | A/B/Z phase signal differential input | ||
I/O | Digital Signal | Input | 8 Configurable optically isolate digital general inputs, 24VDC, 20mA |
Output | 4 Configurable optically isolate digital general outputs, Max. 30VDC,100mA | ||
Analog Signal | Input | 2 Analog inputs, -10 ~ +10V, 12bit | |
Output*1 | 2 Analog outputs, -10 ~ +10V, Max.10mA | ||
Comm Port | USB | Connection with PC for configuration | |
EtherCAT | -EC Control Function Type: EtherCAT Communication | ||
CANopen | -C Control Function Type: CANopen Communication | ||
Front Panel | 4 keys (MODE, UP, DOWN, SET) 5 - digital LED Display | ||
Regeneration Resistor | ● -X Type regenerative resistor ● -N Type 750W Built-in regenerative resistor ● All models can be equipped with external absorption resistors | ||
Control Mode | -EC Control Function Type: CoE(Complies with CiA402 standard), Support PP, PV, TQ, CSP, CSV, CST and HM mode, Full Closed Loop Control Mode *3, Q programs that are pre-stored in the drive can also be started by command -C Control Function Type: Complies with CiA402 standard, Support PP,PV,TQ and HM mode, Full Closed Loop Control Mode*3,Q programs that are pre-stored in the drive can also be started by command | ||
Control Input Signal | Alarm Reset, CW/CCW Limit, Gain Select, Zero Speed Clamp, Emergency Stop, CW/CCW Torque Limit, Speed Limit, General Purpose Input | ||
Control Output Signal | Warning Output, Fault Output, Servo Ready, Velocity Reached, Torque Reached, Position | ||
Protection | Over Current, Over Voltage,Under Voltage, Over Temperature, Bad Encoder Feedback, Over | ||
Dynamic Brake | -X Built in | ||
STO | -X Built in | ||
Weight | M56S-21A8 ■◆:0.8Kg M56S-23A0 ■◆:1.1Kg M56S-24A5 ■◆:1.6Kg M56S-26A0 ■ X:1.9Kg M56S-210A ■ X:1.9Kg M56S-213A ■ X:1.9Kg |
■ Drive Specification -EC—EtherCAT Type -C—CANopen Type 400VAC
Input Power | M56S-313A ■ X M56S-317A ■ X M56S-321A ■ X M56S-326A ■ X | Main Circuit | Three-phase,AC380 ~ 480V ±10%,50/60Hz |
---|---|---|---|
Control Circuit | Single-phase,AC380 ~ 480V ±10%,50/60Hz | ||
Withstand Voltage | Primary to earth: withstand 1800 VAC, 1 min, (Leakage current: 20 mA) [220V Input] | ||
Environment | Temperature | Ambient temperature: 0°C ~ 55°C (If the ambient temperature of servo drive is higher Storage temperature: -20°C ~ 65°C | |
Humidity | Both operating and storage : 10 ~ 85%RH or less | ||
Altitude | Derating is not required for altitudes not higher than 1000m Derating 1% for every additional 100m for altitudes between 1000m and 2000m | ||
Vibration | 9.8m/s2 or less, 10 ~ 60Hz (Do not use continuously at resonance frequency) | ||
Motor Encoder Feedback | ● 23-bit Multi-turn Absolute Optical Encoder ● 21-bit Multi-turn Absolute Magnetic Encoder | ||
Second Encoder Feedback | A/B/Z phase signal differential input | ||
I/O | Digital Signal | Input | 8 Configurable optically isolate digital general inputs, 24VDC, 20mA |
Output | 4 Configurable optically isolate digital general outputs, Max. 30VDC,100mA | ||
Analog Signal | Input | 2 Analog inputs, -10 ~ +10V, 12bit | |
Output | 2 Analog outputs, -10 ~ +10V, Max.10mA | ||
Comm Port | USB | Connection with PC for configuration | |
EtherCAT | -EC Control Function Type: EtherCAT Communication | ||
CANopen | -C Control Function Type: CANopen Communication | ||
Front Panel | 4 keys (MODE, UP, DOWN, SET) 5 - digital LED Display | ||
Regeneration Resistor | Built-in regenerative resistor (All models can be equipped with external absorption resistors) | ||
Control Mode | -EC Control Function Type: CoE(Complies with CiA402 standard), Support PP, PV, TQ, CSP, CSV, CST and HM mode, Full Closed Loop Control Mode, Q programs that are pre-stored in the drive can also be started by command -C Control Function Type: Complies with CiA402 standard, Support PP,PV,TQ and HM mode, Full Closed Loop Control Mode,Q programs that are pre-stored in the drive can also be started by command | ||
Control Input Signal | Alarm Reset, CW/CCW Limit, Gain Select, Zero Speed Clamp, Emergency Stop, CW/CCW Torque Limit, Speed Limit, General Purpose Input | ||
Control Output Signal | Warning Output, Fault Output, Servo Ready, Velocity Reached, Torque Reached, Position | ||
Protection | Over Current, Over Voltage,Under Voltage, Over Temperature, Bad Encoder Feedback, Over | ||
Dynamic Brake | Built in | ||
STO | Built in | ||
Weight | M56S-313A ■ X:1.9Kg M56S-317A ■ X:3.8Kg M56S-321A ■ X:3.8Kg M56S-326A ■ X:3.8Kg |
■ Drive Specification -IP—EtherNet/IP Type -PN—Profinet Type 220VAC
Input Power | M56S-21A8 ■◆ M56S-23A0 ■◆ M56S-24A5 ■◆ M56S-26A0 ■ X | Main Circuit | Single / Three-phase,AC200 ~ 240V ±10%,50/60Hz |
---|---|---|---|
Control Circuit | Single-phase,AC200 ~ 240V ±10%,50/60Hz | ||
M56S-210A ■ X M56S-213A ■ X | Main Circuit | Three-phase,AC200 ~ 240V ±10%,50/60Hz | |
Control Circuit | Single-phase,AC200 ~ 240V ±10%,50/60Hz | ||
Withstand Voltage | Primary to earth: withstand 1500 VAC, 1 min, (Leakage current: 20 mA) [220V Input] | ||
Environment | Temperature | Ambient temperature: 0°C ~ 55°C (If the ambient temperature of servo drive is higher Storage temperature: -20°C ~ 65°C | |
Humidity | Both operating and storage : 10 ~ 85%RH or less | ||
Altitude | Derating is not required for altitudes not higher than 1000m Derating 1% for every additional 100m for altitudes between 1000m and 2000m | ||
Vibration | 9.8m/s2 or less, 10 ~ 60Hz (Do not use continuously at resonance frequency) | ||
Motor Encoder Feedback | ● 26-bit Multi-turn Absolute Optical Encoder ● 21-bit Multi-turn Absolute Magnetic Encoder ● 17-bit Battery-less Multi-turn Absolute Encoder | ||
Second Encoder Feedback*1 | A/B/Z phase signal differential input | ||
I/O | Digital Signal | Input | 8 Configurable optically isolate digital general inputs, 24VDC, 20mA |
Output | 4 Configurable optically isolate digital general outputs, Max. 30VDC,100mA | ||
Analog Signal | Input | 2 Analog inputs, -10 ~ +10V, 12bit | |
Output*2 | 2 Analog outputs, -10 ~ +10V, Max.10mA | ||
Comm Port | USB | Connection with PC for configuration | |
EtherNet/IP | -IP Control Function Type: EtherNet/IP, Modbus TCP Communication | ||
Profinet | -PN Control Function Type: Profinet Communication | ||
Front Panel | 4 keys (MODE, UP, DOWN, SET) 5 - digital LED Display | ||
Regeneration Resistor | ● -X Type regenerative resistor ● -N Type 750W Built-in regenerative resistor ● All models can be equipped with external absorption resistors | ||
Control Mode | 1. Position Mode 2. Velocity Mode 3. orque Mode 4. Full Closed Loop Control Mode *3 5.The pre-stored Q program in the drive can also be started by command | ||
Control Input Signal | Alarm Reset, CW/CCW Limit, Gain Select, Zero Speed Clamp, Emergency Stop, CW/CCW Torque Limit, Speed Limit, General Purpose Input | ||
Control Output Signal | Warning Output, Fault Output, Servo Ready, Velocity Reached, Torque Reached, Position | ||
Protection | Over Current, Over Voltage,Under Voltage, Over Temperature, Bad Encoder Feedback, Over | ||
Dynamic Brake | -X Built in | ||
STO | -X Built in | ||
Weight | M56S-21A8 ■◆:0.8Kg M56S-23A0 ■◆:1.1Kg M56S-24A5 ■◆:1.6Kg M56S-26A0 ■ X:1.9Kg M56S-210A ■ X:1.9Kg M56S-213A ■ X:1.9Kg |
■ Drive Specification -IP—EtherNet/IP Type -PN—Profinet Type 400VAC
Input Power | M56S-313A ■ X M56S-317A ■ X M56S-321A ■ X M56S-326A ■ X | Main Circuit | Three-phase,AC380 ~ 480V ±10%,50/60Hz |
---|---|---|---|
Control Circuit | Single-phase,AC380 ~ 480V ±10%,50/60Hz | ||
Withstand Voltage | Primary to earth: withstand 1800 VAC, 1 min, (Leakage current: 20 mA) [220V Input] | ||
Environment | Temperature | Ambient temperature: 0°C ~ 55°C (If the ambient temperature of servo drive is higher Storage temperature: -20°C ~ 65°C | |
Humidity | Both operating and storage : 10 ~ 85%RH or less | ||
Altitude | Derating is not required for altitudes not higher than 1000m Derating 1% for every additional 100m for altitudes between 1000m and 2000m | ||
Vibration | 9.8m/s2 or less, 10 ~ 60Hz (Do not use continuously at resonance frequency) | ||
Motor Encoder Feedback | ● 23-bit Multi-turn Absolute Optical Encoder ● 21-bit Multi-turn Absolute Magnetic Encoder | ||
Second Encoder Feedback | A/B/Z phase signal differential input | ||
I/O | Digital Signal | Input | 8 Configurable optically isolate digital general inputs, 24VDC, 20mA |
Output | 4 Configurable optically isolate digital general outputs, Max. 30VDC,100mA | ||
Analog Signal | Input | 2 Analog inputs, -10 ~ +10V, 12bit | |
Output | 2 Analog outputs, -10 ~ +10V, Max.10mA | ||
Comm Port | USB | Connection with PC for configuration | |
EtherNet/IP | -IP Control Function Type: EtherNet/IP, Modbus TCP Communication | ||
Profinet | -PN Control Function Type: Profinet Communication | ||
Front Panel | 4 keys (MODE, UP, DOWN, SET) 5 - digital LED Display | ||
Regeneration Resistor | Built-in regenerative resistor (All models can be equipped with external absorption resistors) | ||
Control Mode | 1. Position Mode 2. Velocity Mode 3. orque Mode 4. Full Closed Loop Control Mode, 5.The pre-stored Q program in the drive can also be started by command | ||
Control Input Signal | Alarm Reset, CW/CCW Limit, Gain Select, Zero Speed Clamp, Emergency Stop, CW/CCW Torque Limit, Speed Limit, General Purpose Input | ||
Control Output Signal | Warning Output, Fault Output, Servo Ready, Velocity Reached, Torque Reached, Position | ||
Protection | Over Current, Over Voltage,Under Voltage, Over Temperature, Bad Encoder Feedback, Over | ||
Dynamic Brake | -X Built in | ||
STO | -X Built in | ||
Weight | M56S-313A ■ X:1.9Kg M56S-317A ■ X:3.8Kg M56S-321A ■ X:3.8Kg M56S-326A ■ X:3.8Kg |
■ Safety Certification
- | - | Drive | Motor |
---|---|---|---|
Europe | EMC | EN 61800-3 | EN 60034-1 |
EN 61000-6-2 | |||
EN 61000-6-4 | |||
LVD | EN 61800-5-1 | EN 60034-1 | |
EN 60034-5 | |||
Function Safety (STO) | UL61800-5-2(SIL 3) | / | |
IEC61508(SIL 3) | / | ||
ISO13849-1(PL e) | / | ||
UL Standard | UL 61800-5-1 | UL 1004-1 | |
UL 1004-6 | |||
CSA Standard | C22.2 No.274.13 | CSA C22.2 No.100 |
■ Motor General Specifications
Insulation class | Class F (155℃ ) | Ambient temperature | Working temperature: 0℃ ~ 40℃, Storage temperature: -20℃ ~ 60℃ |
---|---|---|---|
Protection level | IP67 ( Except transfixion part of shaft ) | Humidity | Storage and usage: 20 ~ 85%RH ( no condensation ) |
Installation conditions | Indoor installation, avoiding direct sunlight, corrosive and flammable gas | Altitude | Derating is not required for altitudes not higher than 1000m Derating 1% for every additional 100m for altitudes between 1000m and 2000m |
Vibration | 49m/s2 or less, 10 ~ 60Hz (Do not use continuously at resonance frequency) |
■ Brake Specifications
When the brake is powered on, the armature is retracted, the brake pad is released, and the motor can operate normally. When the brake is powered off, the armature is released, the brake pad is locked, and the motor can't rotate.
Frame | 40mm | 60mm | 80mm | 100mm | 130mm | 180mm | ![]() |
---|---|---|---|---|---|---|---|
Static Friction Torque N·m | 0.32 | 1.5 | 3.2 | 8.0 | 18.5 | 60 | |
Rated Voltage (VDC) | 24 | ||||||
Power Waste (W 20℃) | 6.3 | 7.2 | 9.6 | 14.4 | 24.3 | 52 | |
Current(A) | 0.26 | 0.3 | 0.4 | 0.6 | 1.05 | 2.16 | |
Braking Time | < 70ms (Standard air gap,at 20℃) | ||||||
Release Time | <25ms | ||||||
Release Voltage | 18.5VDC max.(at 20℃) |
■ Shaft Seal
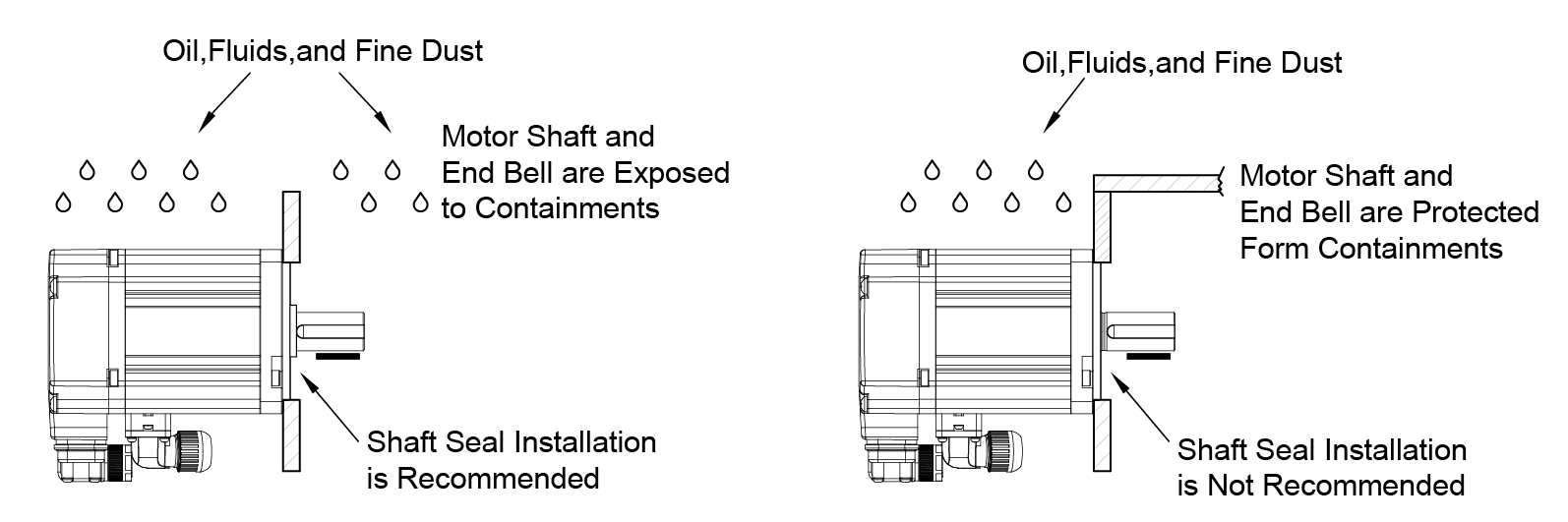
Title | Type | Size(KB) | Download |
---|---|---|---|
M56S Family Brochure_EN20250220-A1 | 6266 |
Title | Type | Size(KB) | Download |
---|---|---|---|
ROHS declaration-2024-A0.pdf | 522 | ||
M56S&M54S Series Drive CE Certification-EMC.pdf | 1659 | ||
M5&M3DV Series Servo Drive CE Certification-LVD.pdf | 1374 | ||
M5 Series Servo Drive SEMI F47 Certification.pdf | 718 |
Title | Type | Size(KB) | Download |
---|---|---|---|
Luna Setup 4.0.24.1130.zip | ZIP | 30628 | |
AMA Servo EtherCAT v3.4.18.zip | XML | 146 | |
CANOPEN_EDS_M56S_V1.0.1.rar | EDS | 8 | |
M56S-IP-V1.4.zip | EDS | 4 |
Filter By Product Type
All ProductsExtended I/O Cables
USB Configuration Cable
CN6/CN7 Communiaction Cable
Motor Types
Regen Clamp
Encoder Output Signal Cable
RS485 Adapter

Delivery & Packaging
Ensure your ordered products are always safely packaged from easy click to fast delivery to your handsProfessional Product Label
Considering all possible harsh application environments, MOONS' specially designed labels for each product, which pass water-resistance test, durability rub test, high temperature resistance and corrosion resistance tests.Besides, our product labels are attached with QR code linking to product details, which is convenient for clients to view the detail product page with their mobile phones.
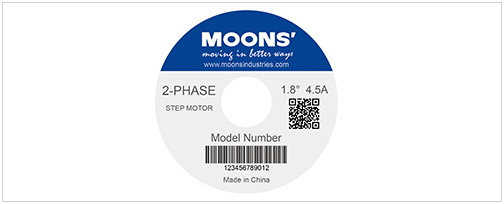
Note: This label design is suitable for products of stepper motor.
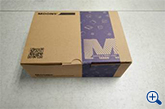
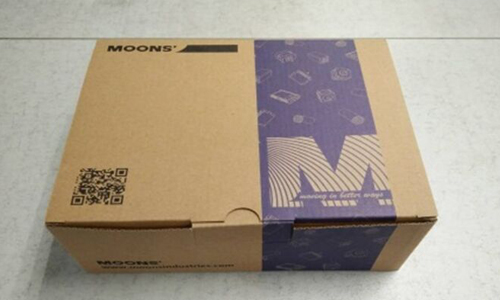
(Professional packing box and unique appearance design)
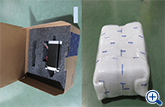
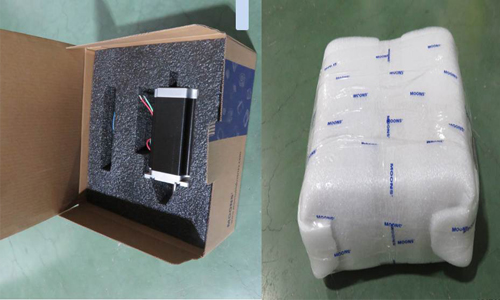
(Single item packed with EPE)
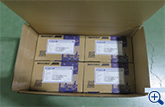
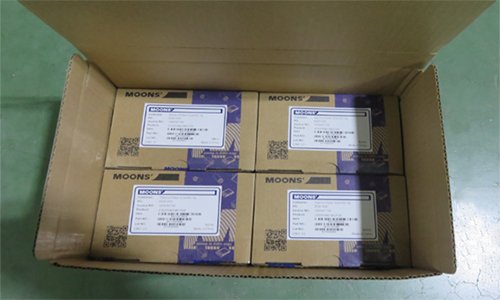
(Multi-products packed with another box)
Safely Packaging
In order to ensure your shipments withstand the long trip and arrive safely and intact, MOONS' specially designed Individual package to pass the drop test with its stable structure.Besides,the package is made from recyclable materials, providing you with professional safety delivery.
Whether just single item or multi-products the clients buy, all products are packed twice to avoid the damage further.
Shipping Visualization
For each case, products are carefully packed by experienced warehouse staff and the key processes are recorded by photos, which are then posted on our website, so that clients could clearly know the packing process and logistics status after placing order.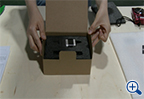
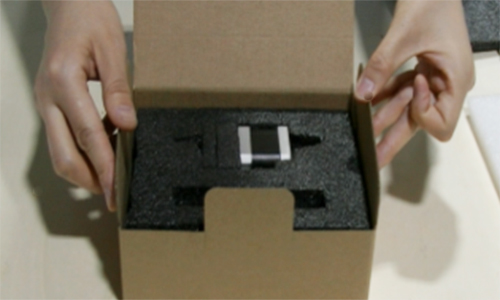
(Product in the box)
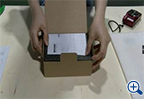
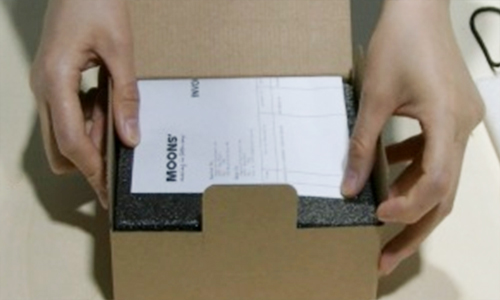
(Add the invoice)
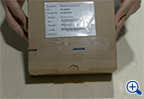
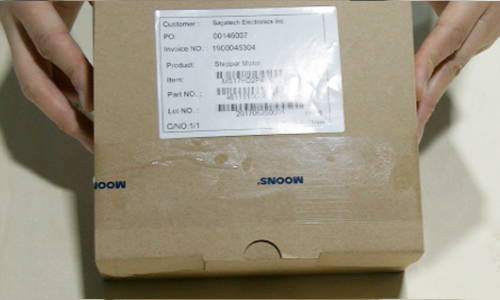
(Label the commodity)
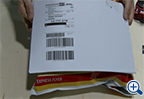
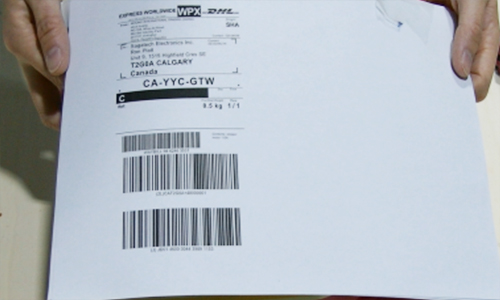
(The logistics waybill attached)
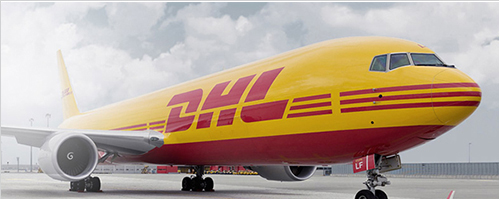
Fast Delivery
Fast Cross-Border DeliveryMOONS' chooses DHL as our main international express shipping partner. As the world's leading logistics specialist, DHL provides our customers with fast and professional inter- national door-to-door delivery service.
Estimated Delivery Time: e.g. China-USA major cities 3 business days.
Professional
Warehouse Management
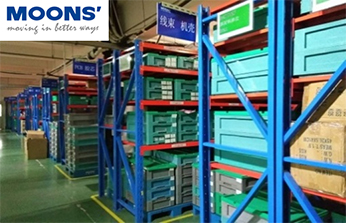