Vacuum Rated Stepper Motors
• AS9100D compliant facility
• Low outgassing
• Optimized power consumption
• Heat dissipation provisions
• Withstand temperature range from-80°C to+200°C
• Low vibration generation
• High amplitude vibration tolerance
• Complete component origin traceability Contact Us for More You've designed the product before, but this time it will be installed in a clean room, vacuum chamber, or perhaps go into space. The operation of any type of electrical device in a vacuum environment is challenging, including stepper motors. There are two specific reasons why conventional stepper motors cannot be used in vacuum environments: heat and contaminants. Heat is generated whenever motor coils are energized. In normal operation, air acts as a conductor and dissipates that heat. In a vacuum, this solution won't work. Our engineers have run into this situation before and have learned to specially wind our motors specifically for vacuum applications. Contaminants - on the microscopic level - show that gas is trapped inside paints, coatings, and greases. As air is removed from the environment, trapped gas inside the motor expands, introducing unwanted contaminants. By using low-outgassing materials in the design and manufacture of our vacuum-rated motors, we have once again minimized outgassing. With the right motor, your design problem becomes a solution. Our expertise comes from seeing almost every type of application imaginable. We will deliver what you need when you need it, and at a price, you can afford.
Temperature Management
No system is 100% efficient, heat is generated while the coils of the motor are energized, and heat becomes problematic while using a conventional motor in a vacuum application for two primary reasons: diminished motor performance, and shortened lifespan of the motor. Heat decreases the magnetic field strength of permanent magnets, resulting in poor motor performance. Motor torque is directly affected by this, and at certain temperatures, the motor will cease to operate. Additionally, heat drastically shortens the lifespan of bearings in your motor, reducing your entire system's lifespan. In a vacuum environment gas is removed leaving little to convect the heat and repeal it away from the motor. Although conventional motor designs take heat convection into account, when a conventional stepper is operated in a vacuum environment, heat quickly builds up and overcomes the motor. For this reason, we have incorporated magnets constructed from alloys with high-temperature tolerance, along with bearings with grease rated from -80°C to 204°C. Additionally, vacuum motors are wound specifically for vacuum applications. Using a specific winding recipe, we developed a motor that generates less heat and provides sustainable performance in vacuums up to 10-7 Torr at 110°C. Outgassing and Contaminations
Expansion of trapped gas inside a motor can introduce unwanted contaminants into the environment, affecting nearby components like sensors and sensitive instruments. In vacuum environments, outgassing must be avoided at all costs. Our vacuum-rated motors are designed to minimize outgassing. The motor components (end caps, stator, rotor, and screws) are made from low-outgassing materials. Special sealed bearings are also incorporated into the design. Additionally, all components are thoroughly cleaned and vacuum baked. A cleanroom environment is used to assemble the motor after it has been baked out, and the package is vacuum sealed to ensure that no contaminants enter the package during transportation. Vacuum Applications
Cleanrooms |
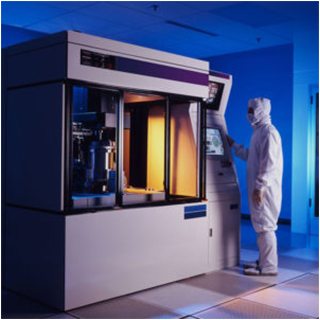 | Since vacuum-rated motors do not introduce contaminants into the environment, they are perfect for sensitive environments where outgassing needs to be avoided, particularly during the semiconductor manufacturing process where even the smallest contamination can ruin the production yield. |
Vacuum chambers |
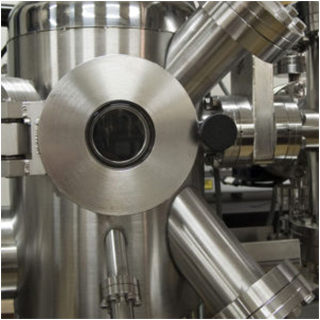 | Vacuum-rated motors are often used in vacuum chambers for testing and manufacturing purposes. |
Space flight |
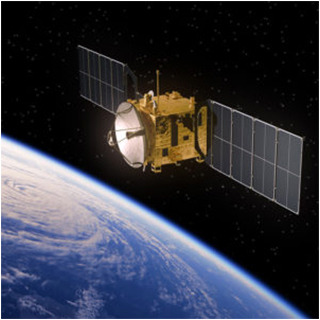 | From communication antennas to vehicle controls, our vacuum-rated motors are specifically designed for satellites and spacecraft. As an AS9100C-registered manufacturer, we manufacture each motor to aerospace standards. |
The following motors are available with the IP67 rating modification:
211 Series |
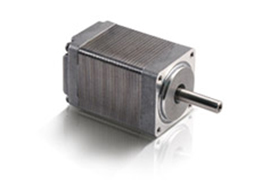 | • NEMA 11 • 1.8 Deg Step Angle • Up to 16.6 oz-in (0.12 Nm) Holding Torque |
4118 Series |
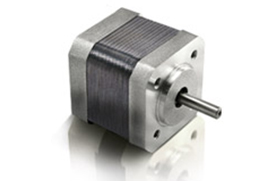 | • NEMA 17 • 1.8 Deg Step Angle • Up to 115 oz-in (0.81 Nm) Holding Torque |
5718 Series |
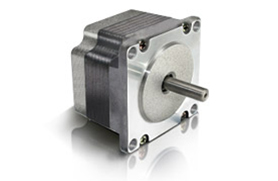 | • NEMA 23 • 1.8 Deg Step Angle • Up to 305 oz-in (2.16 Nm) Holding Torque |
Proprietary Motor Assembly Process
In order to create the cleanest motor on the market, we've created our own motor assembly process and put the results to the test against a known competitor's motor. To do so, we placed our motor into a positive flow chamber (N2 Gas flow 1mm/1min) and measured its outgassing levels over a 72-hour period at a temperature of 125°C. Then we took the following measurements: • Total Mass Loss Percentage (%TML)—The larger the percentage, the more contaminated the specimen.
• Total Mass Loss (ug/motor)—This is the weight of the mass that was evaporated into the chamber from the specimen. The larger the number, the more contaminated the specimen.
Our Results:
About LIN ENGINEERING
LIN ENGINEERING was established in 1987,is the largest manufacturer of the 0.9 degree hybrid step motor in the World. Locates in Silicon Valley, USA where gathers top high-tech enterprises and talents, its' products are mainly applied in Medical instrumentation, high level security monitoring device, aerospace avionics, etc. In 2014, Lin Engineering manufactured 550 thousand pcs 0.9º hybrid stepper motors. June 3rd, 2015 – MOONS' acquired LIN ENGINEERING, INC. of Morgan Hill, CA, which is located in Silicon Valley, USA. It's a milestone that MOONS' will explore North America market further after the acquisition of Applied Motion Products in 2014.